在工业生产环境中,通过有效实施
5S管理可以提高生产效率、改善工作环境并降低浪费。以下是针对车间的5S管理实施指南,并结合一个案例分享:
实施指南:
1.整顿(Sort)
-分析车间内物品及设备,区分必要与非必要物品。
-清理不必要物品,为常用设备创造更多空间。
-设立标准化储存位置,便于快速访问。
2.整理(Setinorder)
-确定每种设备和材料的固定位置,避免混乱和浪费时间。
-标示各项工具和物料的归属位置,方便识别和归纳。
-制定清晰明了的布局图,以优化工作流程。
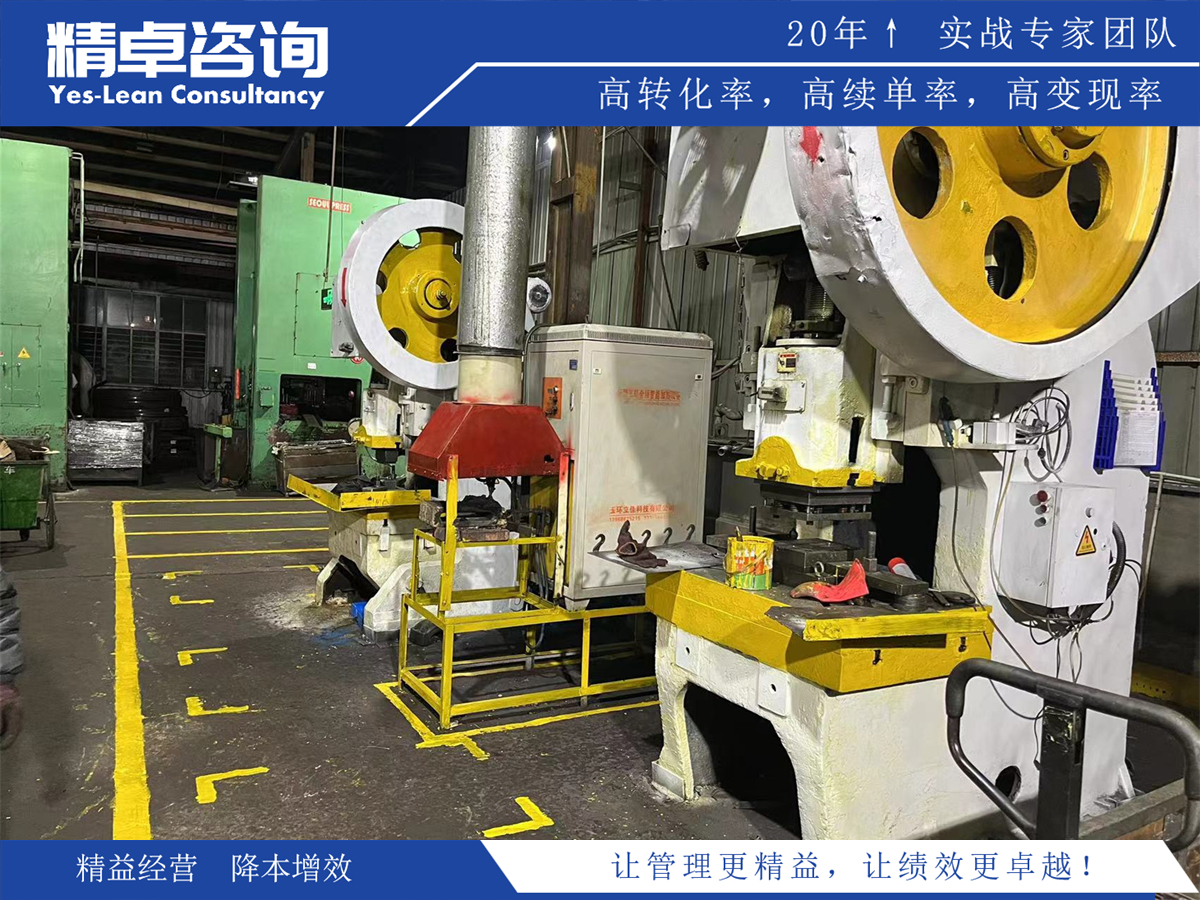
3.清扫(Shine)
-制定日常清洁计划,并确保所有员工参与维护干净整洁的工作场所。
-定期检查设备和工具的清洁状况,及时处理问题。
-强调团队责任感,使清洁成为每个人的习惯。
4.标准化(Standardize)
-建立操作程序手册和标准作业流程(SOP)。
-培训员工遵循统一规范进行操作,并持续强调执行标准化流程的重要性。
-定期审查并更新操作标准以确保其适应现有需求。
5.维持纪律(Sustain)
-建立持续改进机制,鼓励员工自我监督并相互监督。
-设立奖惩机制以激励员工积极参与5S活动。
-将5S文化融入公司价值观中,并持续加强宣传教育。
案例分享:xxx汽车零部件制造厂
xxx汽车零部件制造厂在引入5S管理后取得了显著成效。他们首先进行了全面整顿和整理,清除过剩物品并重新安排设备布局。接着通过建立详细的清洁计划和操作标准来提升车间清洁度和生产效率。同时,公司还投资培训员工学习新的标准化程序,并利用奖励措施激励员工贯彻落实。最后,xxx公司将6S文化渗透到企业DNA中,成功打造了一个高效、安全且令人愉悦的生产环境。
结语:
通过以上实施指南和案例分享可以看出,在车间内推行5S管理可以带来诸多好处,包括提高生产效率、降低事故风险、改善产品质量等。建议企业领导层注重支持力度,在员工中培养起持之以恒地执行5S原则的意识,并不断完善这一管理体系以适应变化环境。