在生产现场管理中,将
5S管理与目视化管理相结合可以进一步提升管理效果和员工参与度。下面探讨5S与目视化管理的整合策略,并通过一个优秀实践案例进行分析:
一、整合策略
1.统一管理目标:
-确定统一的管理目标,将5S管理和目视化管理有机结合,形成整体的生产现场管理体系。
2.标识和标牌整合:
-将5S管理中的标识、标牌和目视化管理中的信息展示工具整合,使标示清晰简洁,信息准确直观。
3.流程优化与可视化:
-在5S整顿过程中优化生产流程,结合目视化管理制作生产流程图,帮助员工直观了解工作流程和作业步骤。
4.问题解决与反馈机制:
-结合5S中的持续改进理念和目视化管理中的问题解决工具,建立员工反馈机制,促进问题快速发现、解决和改进。
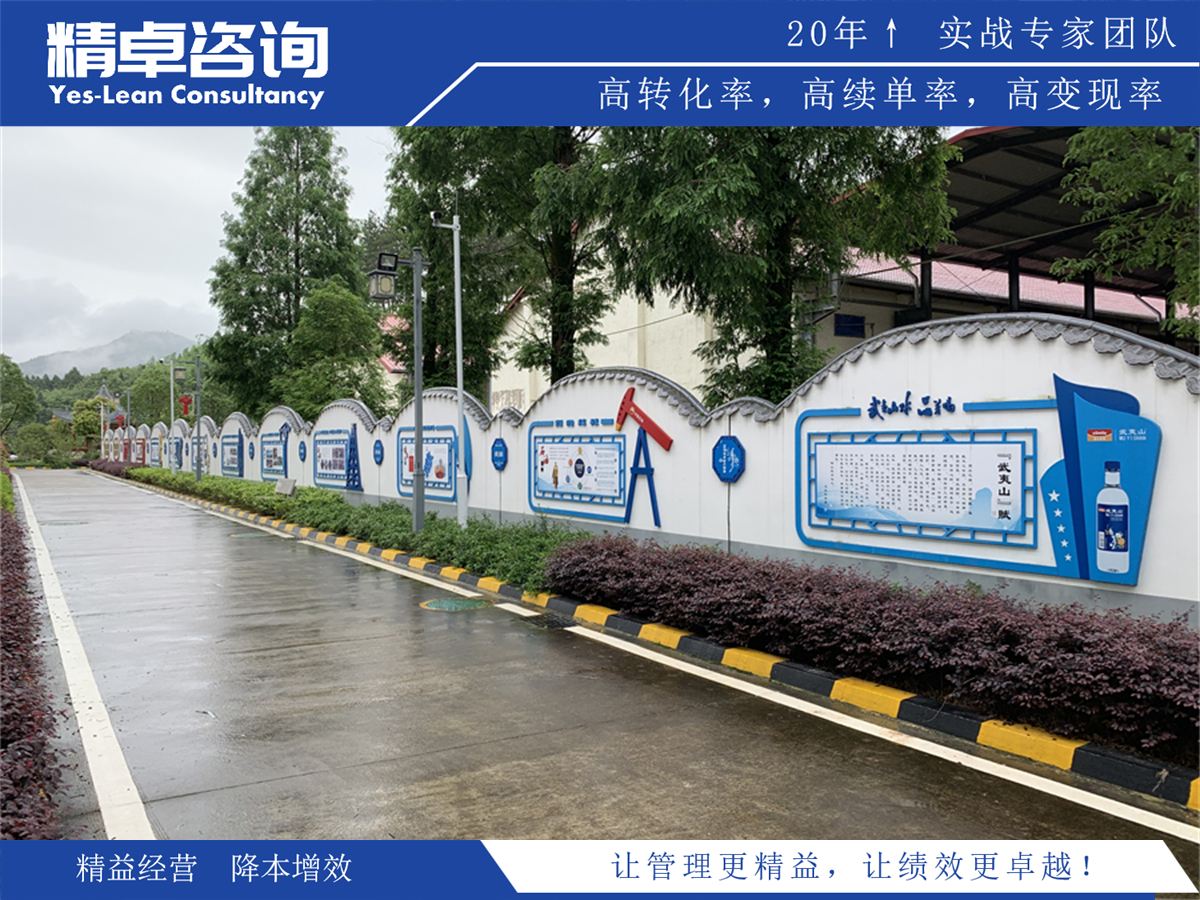
二、优秀实践案例分析
案例名称:XYZ公司生产车间5S与目视化管理整合实践
-背景:XYZ公司生产车间在传统5S管理基础上引入目视化管理,旨在提升生产效率和员工参与度。
-实施措施:
1.标识整合:设立统一的色彩标识系统,清晰标示制度、设备位置和工序要求。
2.看板设置:制作生产进度看板和质量报告看板,实时展示生产情况和质量指标。
3.问题解决卡片:在工作区域设置问题解决卡片板,员工发现问题可即时填写并启动解决流程。
4.员工培训:组织5S和目视化管理知识培训,提高员工对管理体系的理解和执行。
-效果评估:
-生产效率提升:生产进度看板帮助管理层实时监控生产情况,生产效率提升15%。
-错误率降低:标识系统和流程图降低了操作错误率,生产线错误率降低12%。
-安全管理提升:安全标示和安全警示看板有效降低了事故率,安全事故率下降20%。
-持续改进:
-根据员工反馈持续优化管理系统,定期进行5S和目视化管理效果评估,不断改进措施和工具。
三、结论
5S与目视化管理的整合可以有效提升生产现场管理效率和员工参与度,促进持续改进和质量提升。通过整合策略的实施和优秀实践案例的分析,企业可以借鉴成功经验,建立有效的5S与目视化管理整合模式,推动管理水平不断提升,实现生产现场管理的持续优化和效益最大化。