在
精益生产管理中,车间管理的五大基本方法是价值流映射、5S整理、标准化工作、设备管理和单件流。这些方法提供了实用的技巧和策略,帮助企业优化生产流程、提高效率和质量。下面将详细介绍这五大基本方法及其应用技巧:
1.价值流映射
-方法概述:价值流映射是通过绘制价值流图,清晰地展示生产流程中的价值与浪费,从而识别并消除非价值增值活动,实现生产流程优化。
-应用技巧:
-确定价值流的起点和终点,了解产品在生产过程中的具体流动路径。
-识别价值流中的各个步骤,以及其中存在的浪费和瓶颈,制定改进计划。
-与团队合作,持续优化价值流图,以便更有效地管理生产流程。
2.5S整理
-方法概述:5S整理是指整理、排序、清扫、清洁、素养的五个步骤,通过规范工作环境和作业流程,提高生产效率和员工安全。
-应用技巧:
-建立5S标准作业流程,确保所有员工遵守规范和程序。
-定期进行5S检查和持续改进,保持工作环境整洁有序。
-培训员工,提高他们对5S整理的重要性和实施方法的认识。
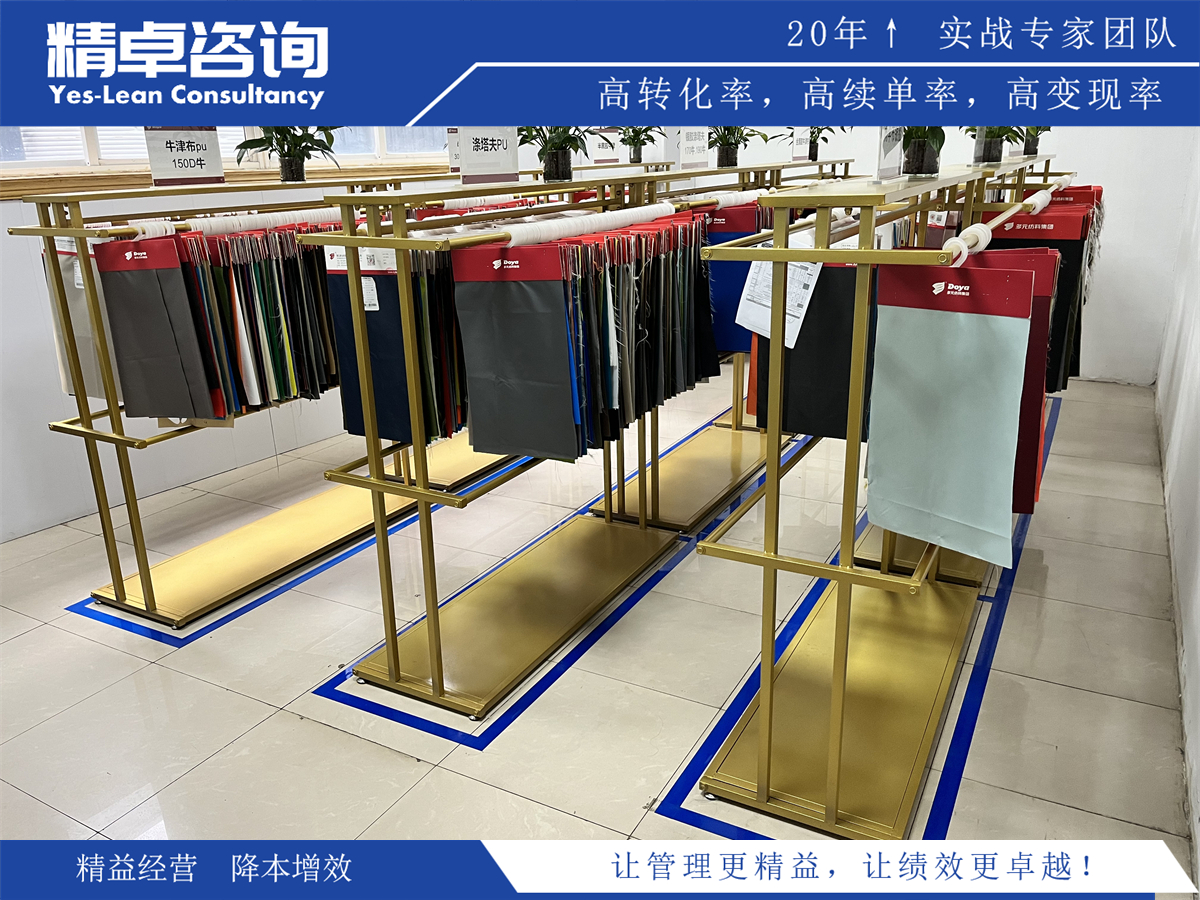
3.标准化工作
-方法概述:标准化工作是制定清晰明确的工作标准和流程,以确保所有员工在工作中保持一致性和高效率。
-应用技巧:
-制定标准作业程序(SOP)并将其贴于工作区,让员工随时查阅。
-建立标准化工作培训计划,确保新员工能够快速熟悉工作流程。
-定期审查和更新标准作业程序,以适应生产环境的变化。
4.设备管理
-方法概述:设备管理是通过有效的设备维护和管理,保障生产设备的正常运行和利用率,降低故障率,提高设备效率。
-应用技巧:
-建立设备维护计划,包括定期检查、保养和维修。
-追踪设备维修记录,并分析故障原因,以预防未来故障的发生。
-培训设备操作人员,提高设备操作技能和维护意识。
5.单件流
-方法概述:单件流是一种生产方式,通过逐件生产,减少库存和等待时间,提高生产效率和灵活性。
-应用技巧:
-优化生产线布局,确保生产流程顺畅无阻。
-实施小批量生产和及时供货,避免过多库存积压。
-定期评估生产线效率,寻找改进点,促进单件流的实施。
通过合理应用价值流映射、5S整理、标准化工作、设备管理和单件流等五大基本方法,企业能够优化生产流程、提高生产效率,以及不断实现精益生产管理的目标。如有任何关于车间管理基本方法的疑问或讨论,欢迎随时在评论区留言,我们乐意为您提供进一步帮助。