6S管理是在5S基础上增加了安全(Safety)这一要素,旨在进一步提高生产效率、质量和安全。以下是企业6S管理实施步骤及效果评估方法的详细解析:
实施步骤:
1.制定计划:
-确定管理层支持,明确目标和范围,制定6S实施计划,并组建6S管理团队。
2.培训与沟通:
-对员工进行6S管理的培训,沟通目标和意义,确保全员参与和理解。
3.第一S:整理(Sort):
-剔除不必要的物品,只保留必要的工具和材料,优化工作场所的布局。
4.第二S:整顿(Setinorder):
-设定明确的放置位置和标准化标识,提高物品的存取效率。
5.第三S:清扫(Shine):
-定期清洁工作场所,保持整洁,并及时修复设备和工具的问题。
6.第四S:清标(Standardize):
-制定和落实5S标准化流程和操作规范,确保工作流程规范化和标准化。
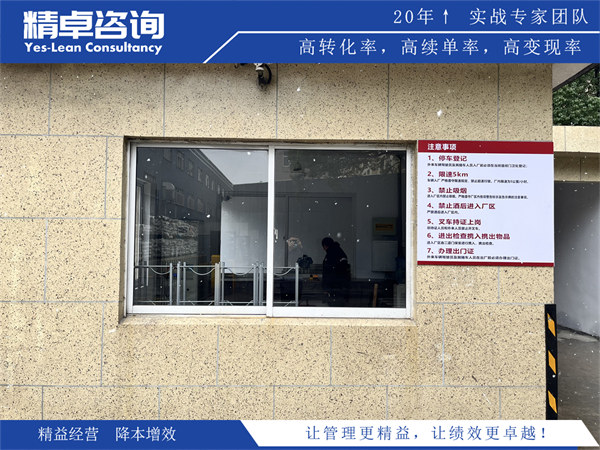
7.第五S:遵守规则(Sustain):
-建立持续改进和自我管理的机制,确保6S管理长期有效运行。
8.第六S:安全(Safety):
-强调安全管理,建立安全意识,推动安全行为规范。确保员工和设备安全。
效果评估方法:
1.KPI指标评估:
-设定关键绩效指标(KPI),如生产效率提升率、生产质量提高率等,定期评估并与目标进行对比。
2.定量数据分析:
-收集数据,分析5S实施前后的生产数据和质量数据的变化,量化6S管理的效果。
3.安全记录分析:
-统计并分析事故率、工伤率等安全记录数据,评估安全管理的提升情况。
4.现场观察与检查:
-定期进行现场观察和检查,评估工作场所的整洁度、规范度和安全性等情况。
5.绩效回顾会议:
-召开绩效回顾会议,与团队共同总结6S管理实施效果,发现问题并制定改进措施。
6.客户满意度调查:
-进行客户满意度调查,了解客户对产品质量与交付效率的感受,以判断6S管理对客户满意度的影响。
结论:
6S管理的有效实施可以提高企业的生产效率、质量和安全,通过明确的实施步骤和科学的评估方法,企业可以全面了解6S管理的实施情况,发现问题并持续改进,推动企业朝着高效、安全和优质的目标前进。