5S管理是一种基于工作场所整理、整顿、清扫、清标和遵守规则的管理方法,旨在提高生产效率、质量和安全,以下是企业5S管理的实施步骤、效益以及案例分析:
实施步骤:
1.制定计划:
-确立管理层支持,明确实施目标和范围,制定5S实施计划,确定参与人员。
2.培训与意识提升:
-对员工进行5S管理的培训,提高员工对5S重要性的认识,营造良好的5S管理氛围。
3.第一S:整理(Seiri):
-剔除不必要的物品和设备,清理工作场所,保留必要的物品,并优化布局。
4.第二S:整顿(Seiton):
-设立清晰的物品放置标准,提高工作效率和生产流程。
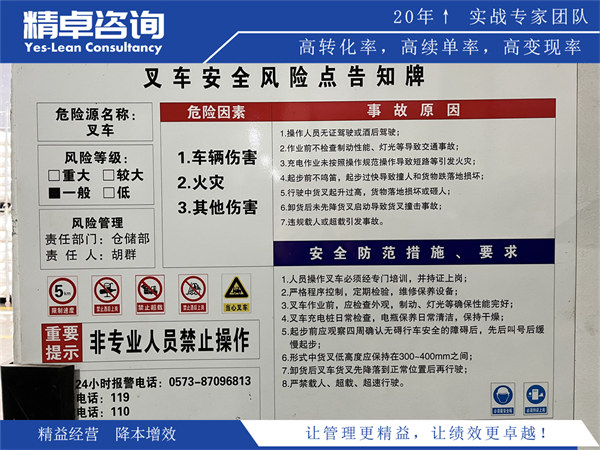
5.第三S:清扫(Seiso):
-清洁和维护工作环境、机器设备,确保设备正常运转和安全作业。
6.第四S:清标(Seiketsu):
-确立5S标准,制定标准化工作程序,促进规范化操作。
7.第五S:遵守规则(Shitsuke):
-建立规章制度,培养员工养成良好的操作习惯和自律精神。
效益:
1.生产效率提升:优化工作场所布局和工作流程,减少无用时间,提高生产效率。
2.质量改善:通过整理、整顿、清洁、清标和规范化操作,减少错误和缺陷,提高产品质量。
3.安全性增强:定期清扫和维护工作环境及设备,减少事故风险,提高员工安全意识。
4.员工参与度提升:促进员工积极参与改进和管理,培养团队合作精神。
案例分析:
公司X是一家制造业企业,实施了5S管理并取得了显著成效。通过整理、整顿、清扫、清标和遵守规则,公司X取得了以下成果:
-生产效率提升了15%,生产线运作更加顺畅。
-产品质量通过5S管理的连续改进得到了提升,不良品率下降了20%。
-工作场所的安全性得到加强,事故率大幅降低。
-员工参与度提高,团队合作精神增强,公司整体氛围更加积极向上。
这个案例展示了5S管理在企业中的实际应用,通过改善工作环境和工作方式,企业不仅提高了生产效率和质量,同时也提升了员工参与度和安全意识,为企业的可持续发展打下了良好基础。