TPM即全员生产维护,是一种以设备为中心展开的现代设备管理理念与方法体系。
一、起源与发展
TPM起源于20世纪70年代的日本,当时日本企业面临着资源短缺和市场竞争激烈的双重压力。为了提高生产效率和产品质量,降低生产成本,日本企业在设备管理领域进行了一系列的探索和实践。TPM理念最初是在日本电装公司(NipponDenso)推行,该公司是丰田汽车的主要零部件供应商。在实践过程中,TPM融合了美国的生产维修理念和日本企业独特的全员参与、持续改进等管理思想,逐渐形成了一套完整的设备管理体系,并在日本制造业得到广泛应用。随着日本企业在全球市场的崛起,TPM也被推广到世界各地,成为众多企业提升设备管理水平的有效工具。
二、核心理念
1.全员参与
-TPM强调从企业高层管理者到一线操作人员,包括设备维修人员、生产主管、质量管理人员等全体员工都要参与到设备管理中来。设备的维护不仅仅是维修部门的责任,每个员工都对设备的正常运行负有一定的责任。例如,在生产车间,操作人员要负责设备的日常清洁、简单检查和基本维护工作,如检查设备的油位、紧固螺丝等;维修人员则负责设备的专业维修和保养;而管理人员则要为设备管理提供资源支持、制定政策和监督执行情况。
2.全系统管理
-它涵盖了设备的整个生命周期,包括设备的规划、设计、选型、购置、安装、调试、使用、维护、修理、改造、更新,直至报废的全过程。例如,在设备规划阶段,就要考虑设备的可靠性、可维护性等因素;在使用阶段,要通过合理的操作和维护,延长设备的使用寿命;在设备报废阶段,要做好设备的拆除、清理和资产处置等工作。同时,TPM还涉及设备管理的各个子系统,如设备档案管理、备件管理、维修计划管理等,通过对这些子系统的有效整合,实现设备管理的整体优化。
3.预防为主
-TPM注重预防性维护,通过对设备运行状态的监测、故障模式的分析和历史数据的统计,提前发现设备可能出现的问题,并采取相应的预防措施。例如,利用设备的状态监测技术,如振动监测、温度监测等手段,实时掌握设备的运行状况。当监测数据出现异常时,及时进行维修或调整,避免设备故障的发生。这种预防为主的理念可以有效减少设备的突发故障,降低设备停机时间,提高设备的可靠性和生产效率。
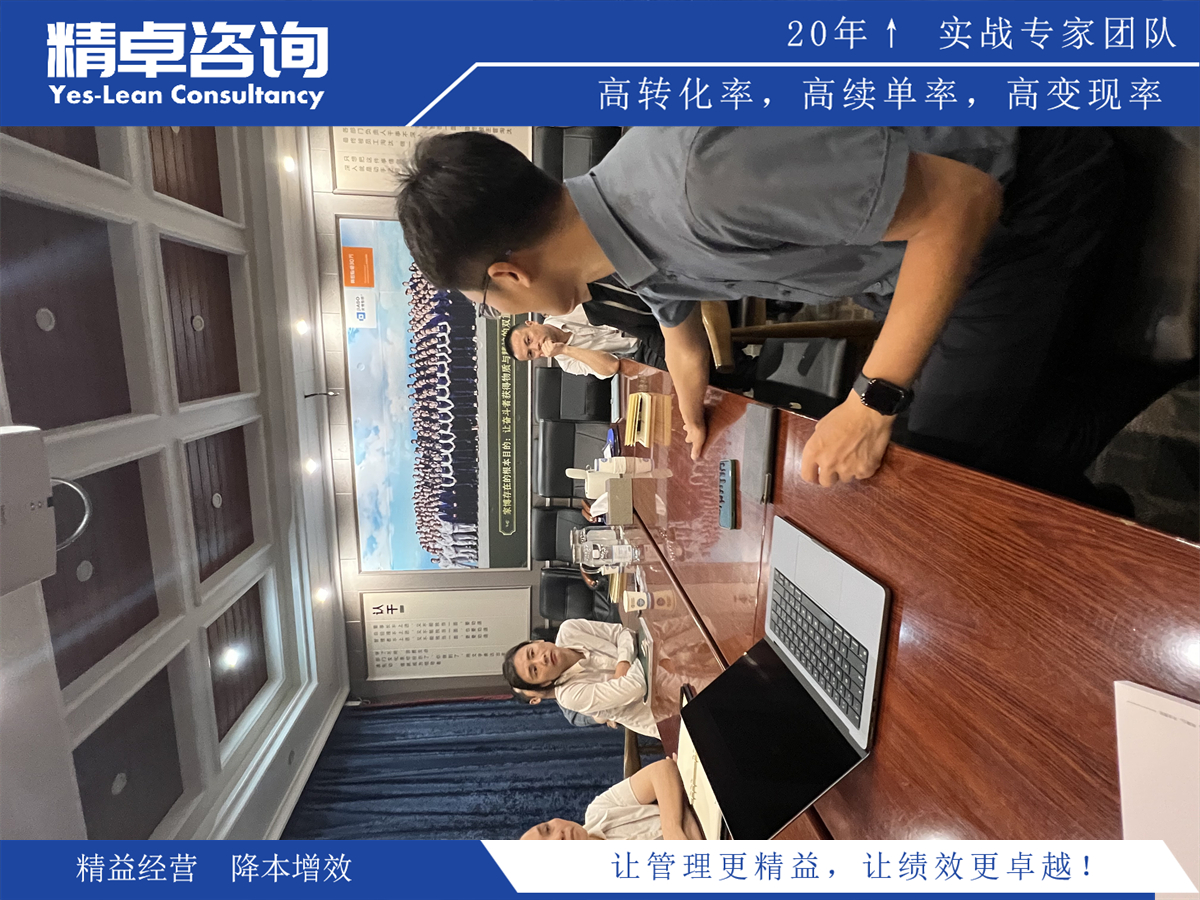
三、目标设定
1.零故障
-这是TPM追求的核心目标之一。通过预防性维护、设备状态监测、员工培训等多种手段,尽可能地消除设备故障。例如,通过定期的设备巡检,及时发现设备的潜在隐患,如磨损的零部件、松动的连接等,并进行及时更换或紧固,从而避免设备故障的发生。在一个成功实施TPM的工厂,设备故障次数会显著减少,设备的可用性大大提高。
2.零不良品
-稳定的设备状态是保证产品质量的关键因素。TPM通过确保设备的精度、稳定性和可靠性,减少因设备原因导致的产品质量问题。例如,在精密机械加工过程中,设备的精度偏差会直接影响产品的尺寸精度和表面质量。通过对设备的定期校准和维护,保证设备的加工精度,从而降低不良品率。
3.零灾害
-强调设备的安全性,在设备的设计、操作和维护过程中充分考虑安全因素,防止因设备故障或操作不当引发的安全事故。例如,在设备周围设置防护栏、紧急制动装置等安全设施,同时对员工进行安全操作培训,确保员工在安全的环境下使用设备。
四、主要活动内容
1.自主维护
-这是TPM的基础活动,由设备的操作人员在日常工作中对设备进行基本的维护工作。包括设备的清洁、润滑、紧固、检查等简单操作。通过自主维护,操作人员可以更好地熟悉设备的性能和运行状况,及时发现设备的异常情况。例如,操作人员在每天开机前对设备进行清洁和简单检查,如检查设备的外观是否有损坏、仪表是否正常等,在工作过程中注意设备的运行声音和温度是否正常,下班后对设备进行清洁和必要的保养。
2.计划维护
-由专业的维修人员根据设备的运行状况、历史故障数据和制造商的建议,制定详细的设备维护计划。包括定期的设备巡检、预防性维护、定期更换易损件以及设备的大修等。例如,维修人员根据设备的运行时间和负荷,定期对设备的关键部件进行检查和维护,如每运行一定时间后对设备的电机进行检查、清洁和保养,对磨损达到一定程度的皮带进行更换等。
3.个别改善
-针对设备运行过程中出现的特定问题或瓶颈环节,成立专门的改善小组进行深入分析和改进。例如,当某条生产线的设备频繁出现故障,影响生产效率时,企业会组织设备工程师、生产主管、操作人员等组成改善小组,通过鱼骨图、5Why等方法分析故障原因,然后制定针对性的解决方案,如对设备的控制系统进行升级、更换易损的零部件等。
4.教育培训
-为了确保全体员工能够有效地参与设备管理,TPM强调对员工进行持续的教育培训。包括设备操作技能培训、设备维护知识培训、TPM理念培训等。例如,企业定期组织员工参加设备操作规范培训,邀请设备制造商的技术专家讲解设备的结构和原理,以及如何进行日常维护和简单故障的排除等知识。
5.初期清扫
-在TPM实施初期,对设备进行全面的清扫是一项重要的活动。通过清扫,不仅可以清除设备表面和内部的灰尘、油污等杂物,还可以在清扫过程中发现设备存在的潜在问题,如泄漏、松动等。例如,在清扫设备时,员工可能会发现设备的某个部位有油液泄漏,这可能是密封件损坏的迹象,从而可以及时进行维修。