TPM是一种以设备保养为核心、全员参与的生产管理方法。在TPM管理实践中,策略优化和持续改进是至关重要的环节,能够帮助企业提高生产效率、降低成本并不断完善运营流程。以下是揭秘TPM管理实践中的策略优化与持续改进:
1.策略优化
1.1设备可靠性分析(FMEA)
-通过对设备可能发生故障模式及其影响进行分析,识别潜在风险点,并制定相应预防措施,以提高设备可靠性。
1.2整合生产计划与设备保养
-将生产计划与设备保养计划相互结合,在不影响生产需求的前提下最大限度地减少停机时间,提高生产效率。
1.3周期性评估和调整
-定期审查现有TPM策略和执行情况,根据反馈结果调整策略或引入新技术、工具以适应变化的需求。
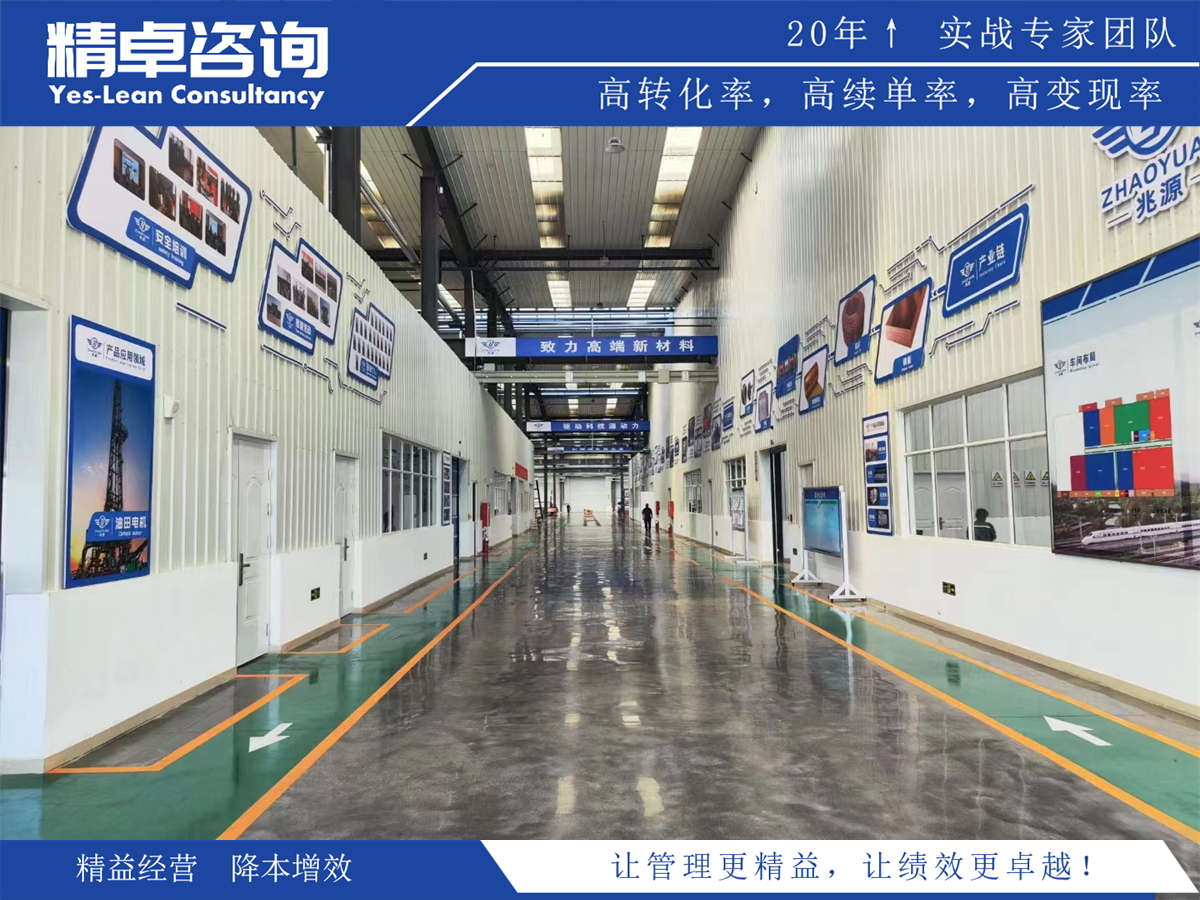
2.持续改进
2.1Kaizen活动推动
-实施Kaizen(持续改善)活动,鼓励员工主动发现问题并提出解决方案,不断完善操作流程和标准。
2.2数据驱动决策
-利用数据分析工具收集和分析相关数据,发现潜在瓶颈或浪费点,并基于数据做出精准决策。
2.3员工培训与参与
-提供系统化的员工培训计划,增强员工技能和意识;鼓励员工积极参与TPM活动,共同促进团队协作和效率提升。
3.成功案例分享
例如某汽车制造公司成功地将TPM理念融入到企业文化中,并通过不断优化设备维护程序、加强人员培训以及推行持续改进活动等措施,取得了显著的效益:减少停机时间、提高产品质量、降低成本并增强竞争力。
总结
在TPM管理实践中,策略优化和持续改进是确保企业顺利实施该方法并取得成功的关键因素。通过不断优化设备保养策略、推行Kaizen活动、加强数据驱动决策以及培训员工参与等举措,企业可以有效地提高生产效率、降低成本并不断追求更高水平的品质和服务。这些努力将使企业处于一个良性循环之中,在竞争激烈的市场环境中保持领先地位。