TPM是一种旨在最大限度地发挥设备潜力、减少故障时间并提高整体生产效率的维护管理方法。它不仅关注设备维护,还包括全员参与、预防性维护和持续改进等方面。以下是对TPM管理的定义以及其核心原则进行探究:
1.定义
TPM是一种通过全员参与、预防性维护和持续改进来实现设备可靠性提升和生产效率优化的管理方法。它强调消除故障根源、提高设备稼动率,并倡导将维护工作融入到日常生产中。
2.核心原则
2.1全员参与
-TPM强调所有员工都应该参与到设备维护和改善过程中,从操作人员到管理层都要共同努力,形成团队合作精神。
2.2预防性维护
-强调采取预防性措施,即定期检查、保养设备,避免突发故障发生,以确保设备处于良好状态并延长使用寿命。
2.3持续改进
-TPM鼓励持续改进思想,不断寻找优化机会并采取行动,以逐步提高生产效率、降低成本和增加价值。
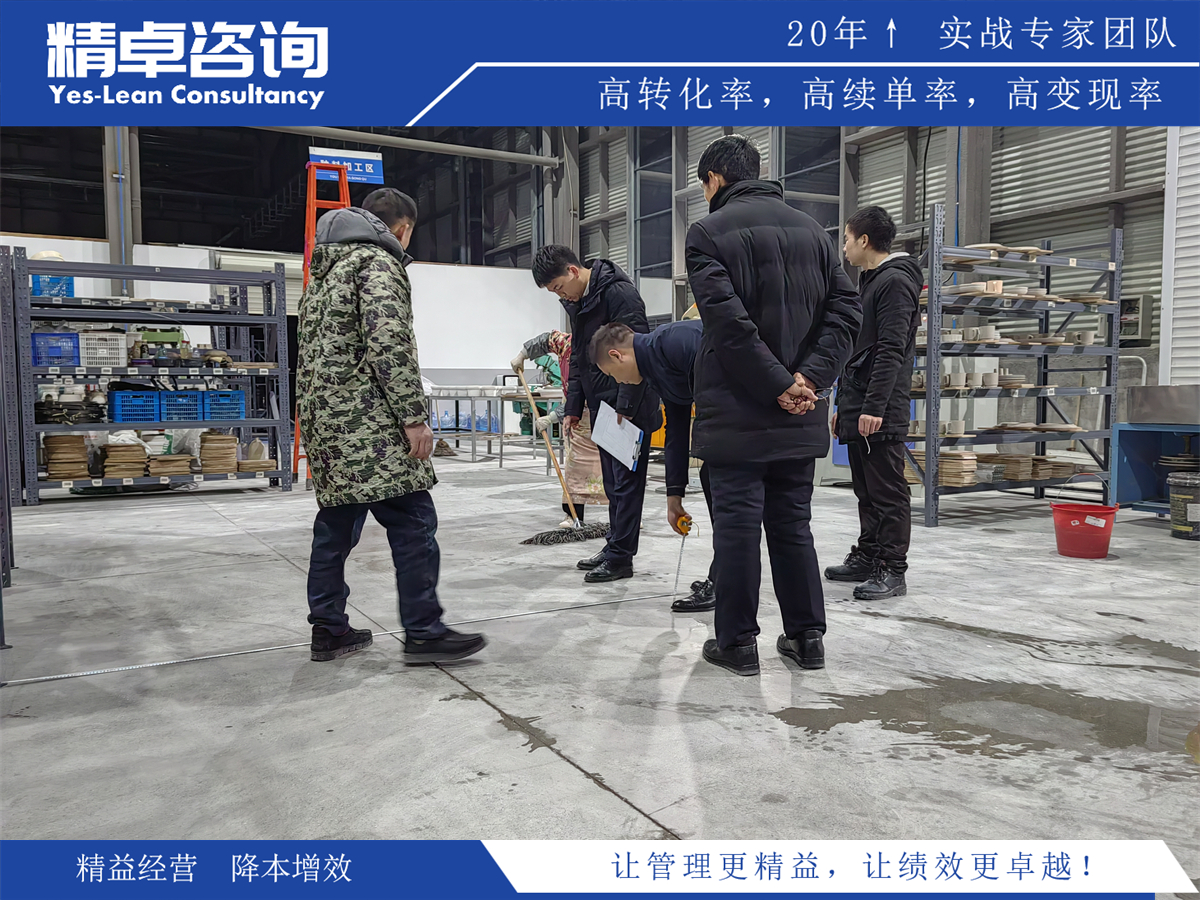
2.45S实践
-5S是TPM的基础之一,包括整理(Seiri)、整顿(Seiton)、清扫(Seiso)、标准化(Seiketsu)和自律(Shitsuke),有助于创造干净整洁的工作环境并提高工作效率。
2.5设备自主保养
-鼓励操作人员负责日常简单保养工作,提高他们对设备状况的认识,及时发现问题并解决。
3.实践意义
-提高生产效率:通过有效的预防性维护和持续改进措施可以降低停机时间,提高设备利用率。
-降低成本:减少计划外停机带来的损失,缩短修复时间节省成本。
-增强安全性:维护良好的设备能够降低事故风险,提升工作场所安全水平。
-促进团队合作:全员参与让团队更加紧密合作,增强沟通与协作能力。
结论
TPM管理方法通过全员参与、预防性维护和持续改进等核心原则,在企业中推动设备可靠性提升、生产效率优化,并营造出积极向上的企业文化。有效实施TPM将为企业带来显著的经济效益和竞争优势。