精益生产是一种旨在通过消除浪费、提高价值创造的管理理念和方法。它强调最大限度地利用资源,以最小的成本满足客户需求。以下是精益生产管理实践及效率优化策略的深入解析。
1.精益生产的核心原则
1.1消除浪费
-定义:识别并消除所有不增加价值的活动,包括过量生产、等待时间、运输、库存、多余加工和缺陷等。
-应用:使用“7种浪费”模型作为分析工具,帮助团队识别各个环节中的浪费,并制定相应对策。
1.2以客户为中心
-定义:从客户需求出发,确保每一项工作都能直接或间接提升客户满意度。
-应用:进行市场调研与反馈收集,以了解客户期望,从而调整产品设计与服务流程。
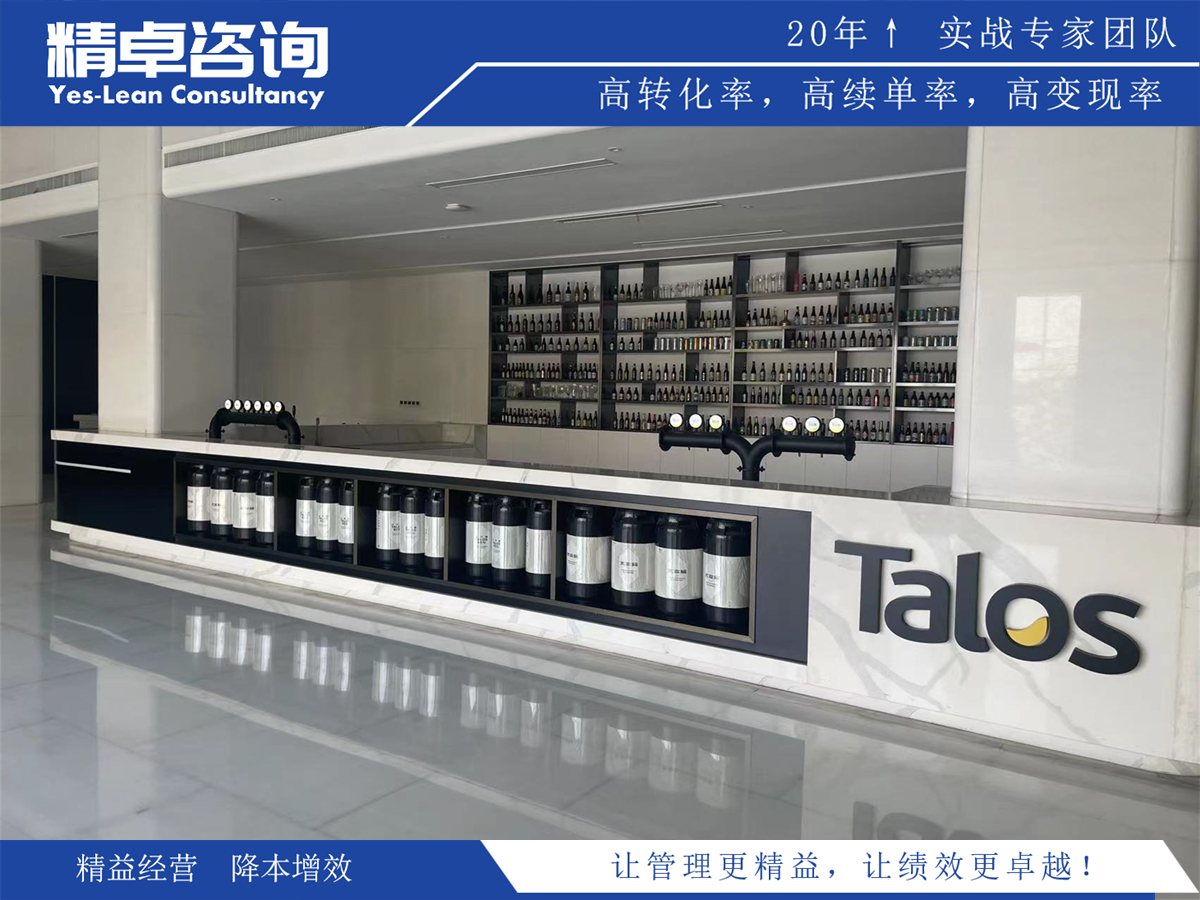
2.精益生产实践
2.1
5S管理-内容:实施整理(Seiri)、整顿(Seiton)、清扫(Seiso)、清洁(Seiketsu)和素养(Shitsuke),改善工作环境,提高员工参与感与责任心。
-效果:提高工作场所的整洁度,有助于减少寻找物品的时间,降低事故发生率。
2.2标准化作业
-目的:创建标准作业程序(SOP),确保每位员工按照最佳方式执行任务,减少变异性,提高一致性。
-效果:通过标准化,提高了操作效率和质量控制,使得新员工能够快速上手。
2.3看板系统
-定义:使用可视化工具,如看板,将信息传递给相关人员,实现按需生产。
-效果:减少库存积压,提高响应速度,同时增强部门之间的信息流通。
3.效率优化策略
3.1持续改进文化(Kaizen)
-概念:鼓励全员参与的小范围持续改进,通过定期召开改进会议来分享经验教训。
-实施例子:设立“改善建议箱”,让员工随时提出改进想法,并给予适当奖励以激励积极性。
3.2数据驱动决策
-方法论:收集关键绩效指标(KPIs)数据,实时监控运营状况,例如设备利用率、产量合格率等。
-应用实例:运用数据分析软件生成报告,为决策提供依据,实现精准管理。
4.风险管控与灵活应对
4.1风险评估机制
-在实施精益生产过程中,对可能出现的问题进行前期评估,如供应链中断、技术故障等,以便及时采取措施应对风险。
5.实施成功案例分享
企业如丰田汽车公司就是精益生产成功实施的典范。其通过有效地将上述原则和实践融入到日常运营中,不仅实现了显著的成本降低,还极大地提升了交付能力和产品质量。这些成功案例为其他企业提供了有力借鉴,也验证了精益生产理论在实际应用中的有效性。
总结
精益生产不仅是一种管理思想,更是一套实用的方法体系,通过消除浪费、关注客户需求以及建立持续改进文化,可以显著提升企业运营效率。在竞争日趋激烈的市场环境下,采用这些策略将有助于企业保持优势,实现长期发展目标。