精益生产是一种以减少浪费、提高价值流动和满足客户需求为核心的生产管理方法。通过优化流程、增加价值、降低成本和提高质量,精益生产已被广泛应用于各行各业。以下是精益生产的原理及应用实例的详细解读:
精益生产原理:
1.价值:
-识别和提供客户愿意支付的产品或服务价值,淘汰对价值没有贡献的活动。
2.价值流:
-分析业务流程,了解从原料采购到最终交付的整个流程,发现并消除不增加价值的浪费。
3.流量:
-通过平衡生产流程,避免生产过剩或拥堵现象,保持生产连续稳定地流动。
4.拉动:
-根据客户需求主导生产,避免过度生产和库存积压,实现按需生产。
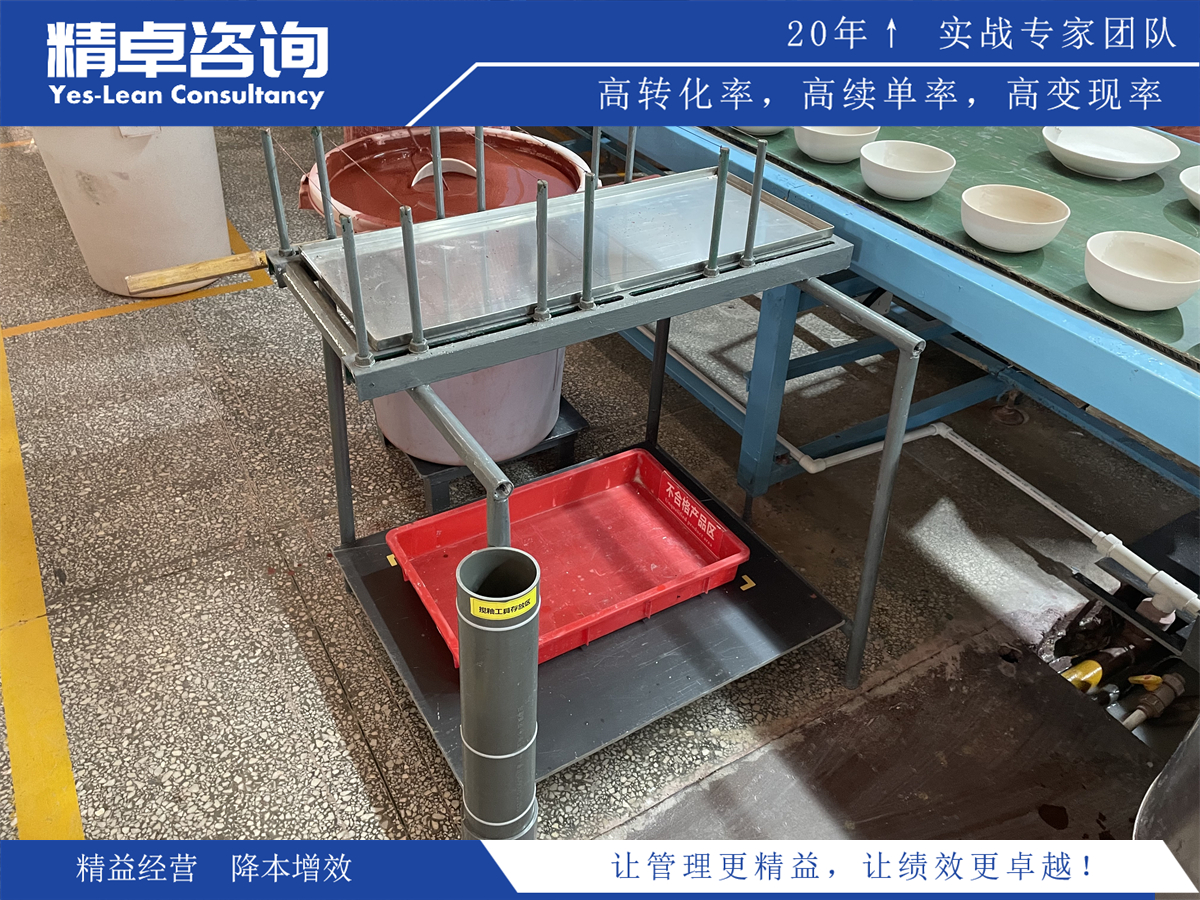
5.追求卓越:
-不断追求卓越,持续改善并寻求最佳实践,促使组织稳步提高绩效。
应用实例详细解读-XYZ汽车零部件制造公司:
挑战分析:
XYZ公司在生产过程中遇到了质量波动大、生产效率低下以及交付周期较长等问题,需要改善生产管理方式以提高竞争力。
精益生产应用实例:
1.价值流分析:
-通过分析生产流程,识别从原料采购、生产加工到出货的价值流,发现生产过程中的不必要浪费,如等待时间、运输浪费等,并进行优化。
2.流程优化:
-引入Kanban系统优化生产流程,明确工作任务和流程顺序,降低库存积压,提高生产效率。
3.质量管理优化:
-实施精益工具如5S、Poka-Yoke(防错装置)等,提高生产线质量管理水平,降低次品率。
4.培训和技能提升:
-开展员工培训计划,提升员工技能和素质,使其更好地适应新的生产管理模式并承担更多责任。
5.持续改进:
-成立持续改进小组,定期收集员工改进建议,积极解决生产中的问题,并持续优化生产流程。
成果展示:
通过精益生产方法的应用,XYZ公司取得了一系列成果:
-生产效率提高了20%,产能得到明显提升。
-产品质量稳定,客诉率显著下降。
-交付周期缩短了30%,客户满意度得到提升。
-成本控制更加有效,盈利能力明显增加。
以上案例展示了精益生产方法在实际企业中的应用和成果,通过不断优化流程、提高价值和培养团队参与意识,企业可以提高生产效率、质量和客户满意度,实现持续增长和成功。希望这个实例能为您提供灵感和启示。