精益生产是一种以最大限度减少浪费为核心的生产管理理念,旨在提高生产效率、质量和客户满意度。以下是对精益生产的核心原则解析并提供实践指南:
核心原则解析:
1.价值观念(Value):
-核心概念:确定产品或服务的价值,从客户角度界定。
-实践指南:
-理解客户需求并精确定义价值。
-识别客户愿意为其付费的特定产品或服务特征。
2.价值流程(ValueStream):
-核心概念:识别产品或服务价值流中的活动,并消除非价值增添环节。
-实践指南:
-映射整个价值流程,找出浪费并优化。
-改进流程以最大程度地提供价值。
3.流程化(Flow):
-核心概念:优化价值流程中的流动,避免停滞和等待。
-实践指南:
-简化流程,使工作顺畅无阻。
-实施“单块流程”以提高质量和效率。
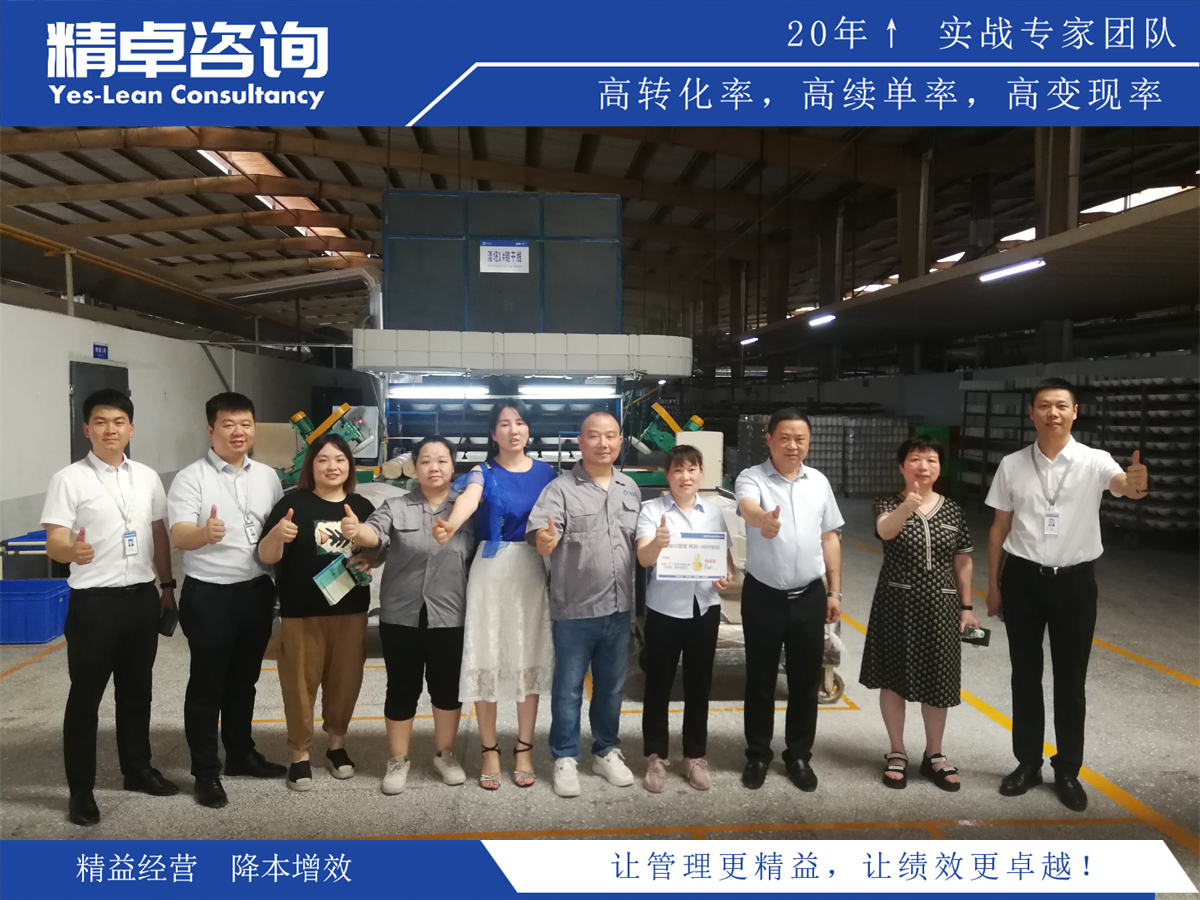
4.拉动制作(Pull):
-核心概念:根据需求拉动生产,避免过度生产和库存。
-实践指南:
-基于客户需求调整生产计划。
-制定“按需生产”方式,确保产品按需生产。
5.追求完美(Perfection):
-核心概念:持续追求完善、连续改进,永不停歇。
-实践指南:
-培养持续改进的文化。
-定期评估并优化生产流程。
实践指南:
1.价值流映射:
-分析并绘制整个价值流程图,识别浪费的环节。
2.持续改进文化建立:
-培养员工持续改进的意识,鼓励提出改进建议。
3.精益生产工具应用:
-应用精益生产工具,如Kanban、5S等,优化生产流程。
4.敏捷生产实践:
-结合敏捷方法,实现快速反馈和灵活生产。
5.定期评估与调整:
-定期评估生产效率和质量,及时调整生产策略,持续改进。
案例分析:
案例背景:一家制造企业引入精益生产模式,着重强调核心原则的实践。
核心措施:
1.价值流映射实践:
-通过价值流映射,发现原材料采购流程中的瓶颈,并优化供应链管理。
2.持续改进文化建立:
-培养员工提出改进建议的氛围,定期举办改进活动,推动持续改进。
成果展示:
-降低生产成本:优化供应链流程导致原材料管理更加高效,生产成本降低了10%。
-提高交付效率:引入拉动式生产使得交付效率得到提升,并减少了库存积压。
-质量提升:持续改进文化的建立使得产品质量和客户满意度得到提升。
通过以上案例分析和实践指南,企业可以更好地理解精益生产的核心原则,并在实践中取得显著成效,从而提高生产效率、质量和客户满意度。