精益生产管理是一种通过减少浪费、优化流程、提高效率和质量的管理方法。以下是精益生产管理的实践指南以及效果评估解读。
实践指南:
1.
5S管理实施:
-整理(Sort):去除不必要的物品,保持工作区整洁有序。
-整顺(Setinorder):将必要物品定位妥当,方便工作人员取用。
-清扫(Shine):定期清洁工作区,保持设备和环境清洁。
-清洁(Standardize):制定标准化清洁流程,并让全体员工执行。
-保持整洁(Sustain):培养员工良好习惯,持续保持整洁。
2.持续改进:
-建立持续改进的文化,鼓励员工提出改进建议,定期评估生产流程并进行优化。
3.价值流映射:
-分析整个价值链,识别价值与非价值流活动,找出并消除浪费。
4.拉动生产:
-根据客户需求进行生产,避免过度生产和库存积压,提高生产效率。
5.标准化工作流程:
-建立标准化的工作流程,确保每个环节执行一致和高效。
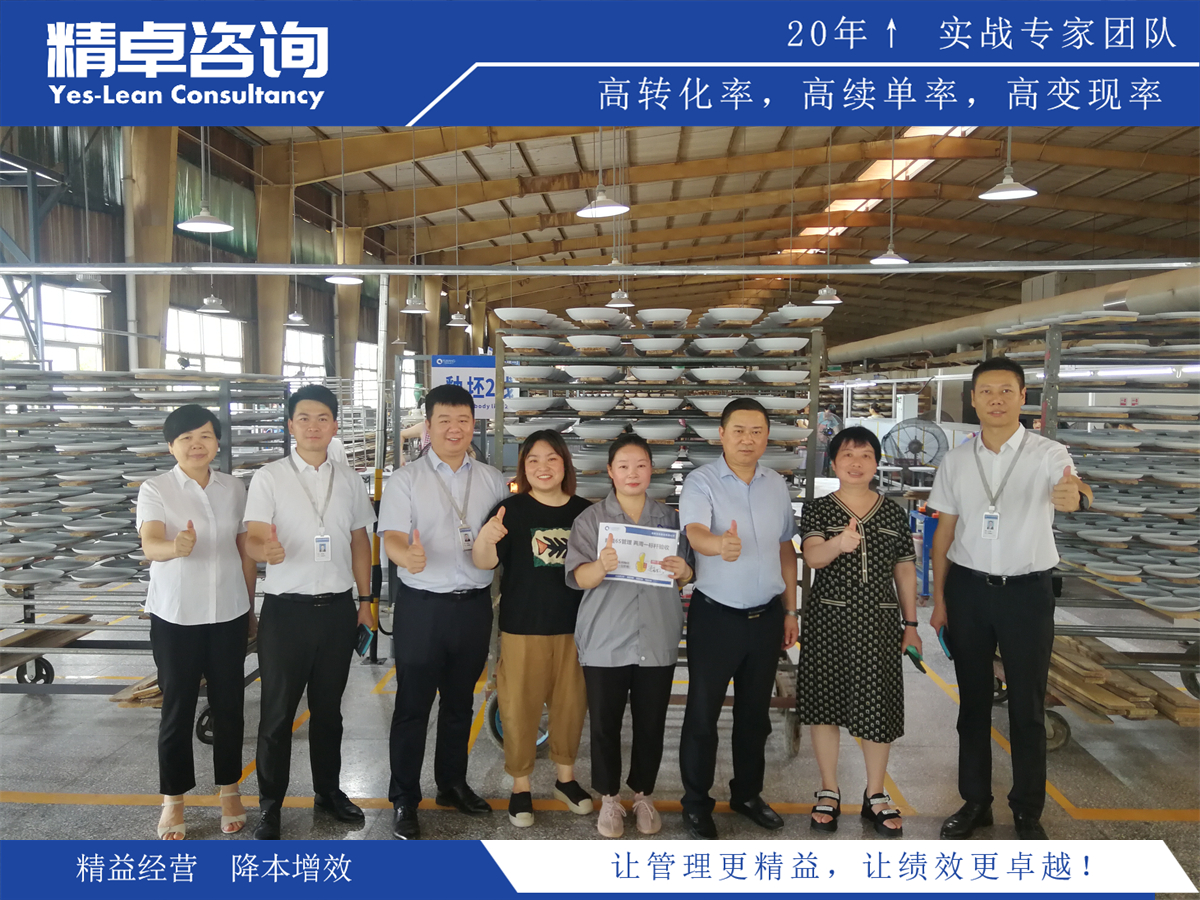
效果评估解读:
1.生产效率提升:
-通过精益生产管理实践,生产效率得到提升,产品制造时间缩短,产量增加。
2.质量水平提高:
-实施精益生产管理后,产品质量得到提升,缺陷率降低,客户投诉减少。
3.成本优化:
-消除浪费、优化流程和提高效率后,生产成本得以降低,企业盈利能力提升。
4.员工参与度增加:
-建立持续改进的文化和鼓励员工提出改进建议,提高员工主动参与度和团队合作精神。
5.客户满意度提升:
-通过提高生产效率和质量,按时交付产品并满足客户需求,客户满意度得到提升。
案例分析:
案例背景:一家电子制造公司引入精益生产管理实践,以提高生产效率和质量。
核心措施:
1.5S管理实施:
-建立5S管理体系,定期进行工作区域整理、整顺、清扫、清洁和保持整洁,提升工作效率。
2.持续改进文化建立:
-鼓励员工提出改进建议并持续改进生产流程,定期举办改进活动,激励员工参与。
成果展示:
-生产效率提升了15%。
-产品质量指标提升,缺陷率降低了10%。
-成本控制得到改善,生产成本降低了8%。
-员工参与度增加,工作环境更加整洁有序,客户对产品质量和交付准时性评价提升。
通过以上实践指南和效果评估,企业可以有效实施精益生产管理,并通过持续改进和优化取得更好的业绩和生产效果。