工厂6S管理是如何实现降本增效的?什么是6S管理,6S现代企业管理模式,这一管理法首先在日本的企业应用。由于整理(Seiri)、整顿(Seiton)、清洁(SeiketSu)、规范(Standard)、素养(ShitSuke)的日语罗马拼音均以S开头,故zui早简称5S管理。我国企业在引进这一管理模式时,另上了英文的安全(Safety),因而称6S管理法。
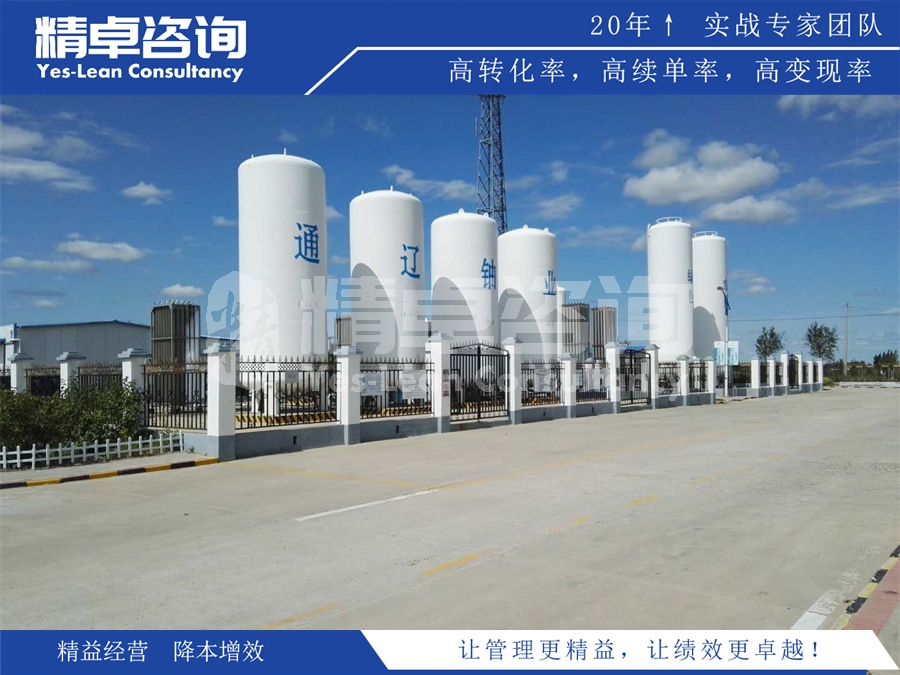
6S培训
一、6S管理简介
6S管理源于日本企业对5S管理的扩展,顾名思义,就是对现场整理、整顿、清扫、清洁、素养、安全六个方面的管理。
整理
将工作现场的所有物品区分为有用品和无用品,除了有用的留下来,其它的都清理掉。
整顿
把留下来的必要用的物品依规定位置摆放,并放置整齐加以标识。
清扫
将工作场所内看得见与看不见的地方清扫干净,保持工作场所干净、亮丽,创造良好的工作环境。
清洁
将整理、整顿、清扫进行到底,并且制度化,经常保持环境处在整洁美观的状态。
素养
每位成员养成良好的习惯,并遵守规则做事,培养积极主动的精神(也称习惯性)。
安全
重视成员安全教育,每时每刻都有安全第一观念,防范于未然。
6S管理是指运用系统的理论基础和辩证唯物主义,正确处理人、物、地、信息之间的关系,从而得出科学的管理方法。近年来,现场管理的理念和方法被国内多家企业采用和推广,并取得了成效。
工厂全面推行6S管理活动,要求工厂全体员工参与定期整理、定期整顿、定期清扫、定期清洁,保障工厂员工区生活区、作业去、生活环境的安全,这也是一项提高识字率的管理活动。
二、6S管理对工厂降本增效的促进作用
事实证明,实施工厂6S管理后,工厂在降本增效方面确实有了很大的提升和改善。具有很好的推广效果,主要表现在以下几个方面。
1、实施6S管理可以从安全上降低设备的成本和收益。
工厂实施6S管理后,加强了对其内部消防、厨房、客房、停车场等经营区域所有设施设备的清扫、清洁和保养,并定期进行安全检查,确保一切安全时落实防控措施,及时消除安全隐患,确保工厂一直在安全运行状态。
更重要的是,让工厂设备管理人员有更多的精力去研究降低设备消耗的工作。
2、6S管理的实施,夯实了降本增效的基石。
工厂实施6S管理,首先要改善原工作现场标准化的不足,多余物品从生产现场移除。
但清理并不是简单的拆掉后扔掉,而是要评估一下你面前没用的物品的价值,有些有价值的东西可以通过各种方式变废为宝。
3、实施6S管理,精细化成本管理,增加效益。
工厂实施6S管理后,员工个人素质提升由此,个人的责任感和敬业精神得到了增强,降本增效的意识也得到了更多的重视和强化,特别是在工厂经营管理过程中,每一个细节都必须细心管理。
例如,餐饮部的后厨,注重食材的综合利用,将剩余的食材物尽其用,杜绝浪费,zui大限度降低运营成本。
又如:为了降低原材料采购成本,尤其是日常消耗量大的原材料,在保证质量的前提下,采购部员工不计较麻烦,在一个广泛的市场,并坚持交货。与几家公司的原则相比,批量清单还采用了招标制,大大降低了原材料成本,扩大了经营效率的利润空间。
4、通过6S管理,提升形象,增加经济附加值。
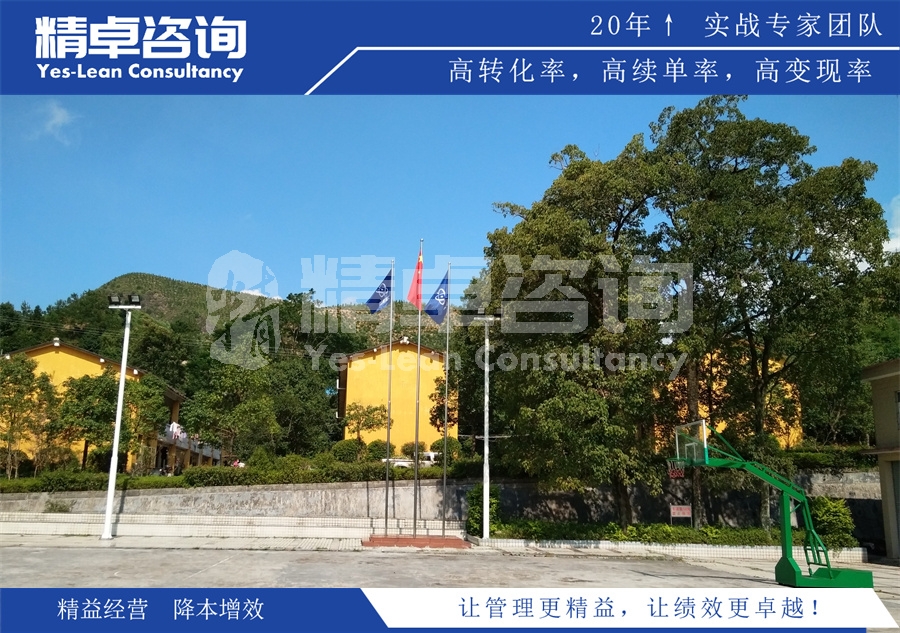
实施6S管理后,工厂管理更加规范,使工厂处处保持整洁干净的现场环境,时刻宣传精力充沛的员工优质的服务态度,大大提高了客户满意度,吸引了更多回头客和合作伙伴。与工厂长期合作,工厂营业收入可开源。
工厂实施6S管理,提高了生产效率,让员工在经营过程中能够快速找到使用频率高的物料,从而节省时间,降低提供服务的成本。通过6S管理,员工有了归属感,增强了责任感和职业道德,更加敬业,也为工厂降本增效带来了实实在在的提升。
工厂6S管理是如何实现降本增效的?以上就是6S培训公司的相关介绍,做好企业的6S管理工作就是为精益生产管理活动打下基础,让精益生产管理在企业中发展有一个良好的前提。