硫化车间
5S管理内容和标准在现代制造业中,5S管理是一种关键的生产和组织方法,特别在硫化车间的应用。5S管理方法旨在优化工作环境,提高生产效率,减少资源浪费。本文将深入探讨硫化车间中的5S管理,包括其内容和标准。
第一章:硫化车间中的5S管理概述
什么是
5S管理体系?
5S管理是一种源自日本的管理方法,代表整理(Seiri)、整顿(Seiton)、清扫(Seiso)、清洁(Seiketsu)和素养(Shitsuke)。这五个步骤的目标是创造一个整洁、有序、高效且安全的工作环境。
第二章:硫化车间中的5S管理重要性
5S管理对硫化车间的影响
硫化车间涉及许多设备、工具和材料,因此通过实施5S管理,可以zui大限度地优化工作流程,提高生产效率。
整理(Seiri)
整理步骤的目标是辨识和清除车间中不必要的设备、材料和工具。这将减少混乱,提高工作效率。
整顿(Seiton)
整顿意味着为每个工具和材料分配明确的储存位置。这有助于员工快速找到所需物品,从而减少生产中的停顿。
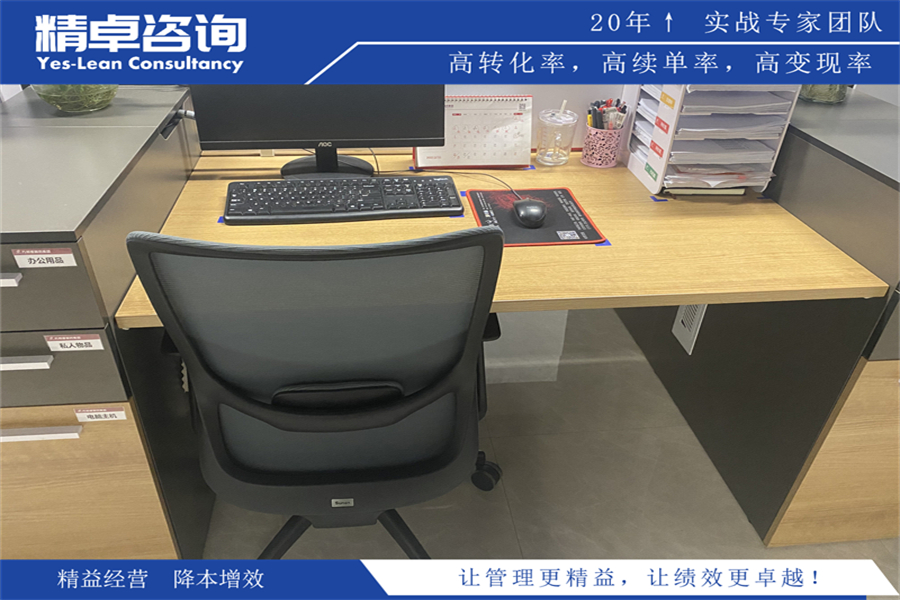
清扫(Seiso)
保持硫化车间的清洁和整洁是5S管理的重要组成部分。定期清理有助于创造更安全和舒适的工作环境。
清洁(Seiketsu)
清洁步骤旨在维持标准化的工作环境。通过使用明确的标识和标志,确保所有员工都能遵循相同的整理标准。
素养(Shitsuke)
素养阶段强调长期维护
5S标准的重要性。培训和监督有助于确保员工始终遵循zui佳实践,保持良好的工作环境。
第三章:硫化车间5S管理的优势
提高生产效率
通过减少搜索时间和减少混乱,5S管理可以显著提高工作效率和产能。
减少资源浪费
整理和整顿步骤有助于减少不必要的库存和物品,从而减少资源和时间的浪费。
改善产品质量
保持清洁和整洁的工作环境有助于减少错误和缺陷,从而提高产品质量。
增强安全性
清扫和整顿步骤有助于减少事故和伤害的风险,为员工创造更安全的工作环境。
第四章:硫化车间5S管理的实施步骤
评估现状
了解硫化车间的当前状态和问题,为实施5S管理做好准备。
制定计划
制定详细计划,明确实施5S的时间表、责任分工和预期成果。
员工培训
向员工传达5S管理的概念和好处,确保每个人都理解和支持这种方法。
逐步实施
逐步按照5S的步骤进行实施,确保每个阶段的平稳过渡。
持续改进
定期评估5S管理的效果,寻找改进的机会并持续优化工作环境。
第五章:硫化车间5S管理的挑战与解决方案
员工参与度
员工可能会对新的管理方法产生抵触情绪,解决方法包括明确好处并提供培训。
维持5S标准
持续维持5S标准需要全体员工的共同努力,可以通过设立奖励机制来鼓励积极参与。
1、生产的布置5S管理要符合生产工艺的要求,便于员工操作,尽量减少员工的行走距离;同时要符合安全生产和节约生产面积的要求。
2、各种物品都应有适当固定的存放地点,符合员工的操作顺序,便于员工使用和拿放。
3、毛坯、工具、用具和控制装置应尽量布置在员工正常的和zui大的工作区域内,使员工能以zui短的距离,zui少的时间和zui小的体力消耗进行操作。
4、物品放置的高度、工作台和工作椅的高低都要适合操作员工身体的特点,使员工在操作时或拿放物品时,尽量不弯腰、不踮脚、不歪身。
5、现场地上多余的和不必要的物品应及时清理,以免造成现场的过分拥挤,影响员工的正常生产活动。
6、必须满足生产工艺对工作环境的要求,比如有些工艺要求恒温、恒湿等。
结论
在硫化车间中实施5S管理是提高效率、减少资源浪费、改善质量和增强安全性的有效方法。透过逐步实施5S方法,企业可以创造一个更有序、更清洁且更高效的工作环境。