纺丝车间
5S管理内容和标准,在纺丝车间,
5S管理培训是一种关键方法,可以显著提高生产效率、产品质量以及员工的工作环境。通过整理(Seiri)、整顿(Seiton)、清扫(Seiso)、清洁(Seiketsu)和素养(Shitsuke)五个步骤,纺丝车间可以创建一个有序、高效和安全的工作环境。以下是纺丝车间5S管理的具体内容和标准,以实现持续改进和卓越绩效。
1. Seiri(整理):
整理阶段旨在清除纺丝车间内不必要的物品,减少杂乱,提高工作效率。这包括:
辨别并清除过期、损坏或闲置的设备、原材料和工具。
保留只有在纺丝过程中真正需要的物品,减少占用空间。
2. Seiton(整顿):
整顿步骤旨在优化工作区域的布局,使之更加整洁和有序。操作包括:
设计合理的储存系统,确保每个物品都有固定的存放位置。
使用标识、标签等方式,使物品易于识别和分类。
3. Seiso(清扫):
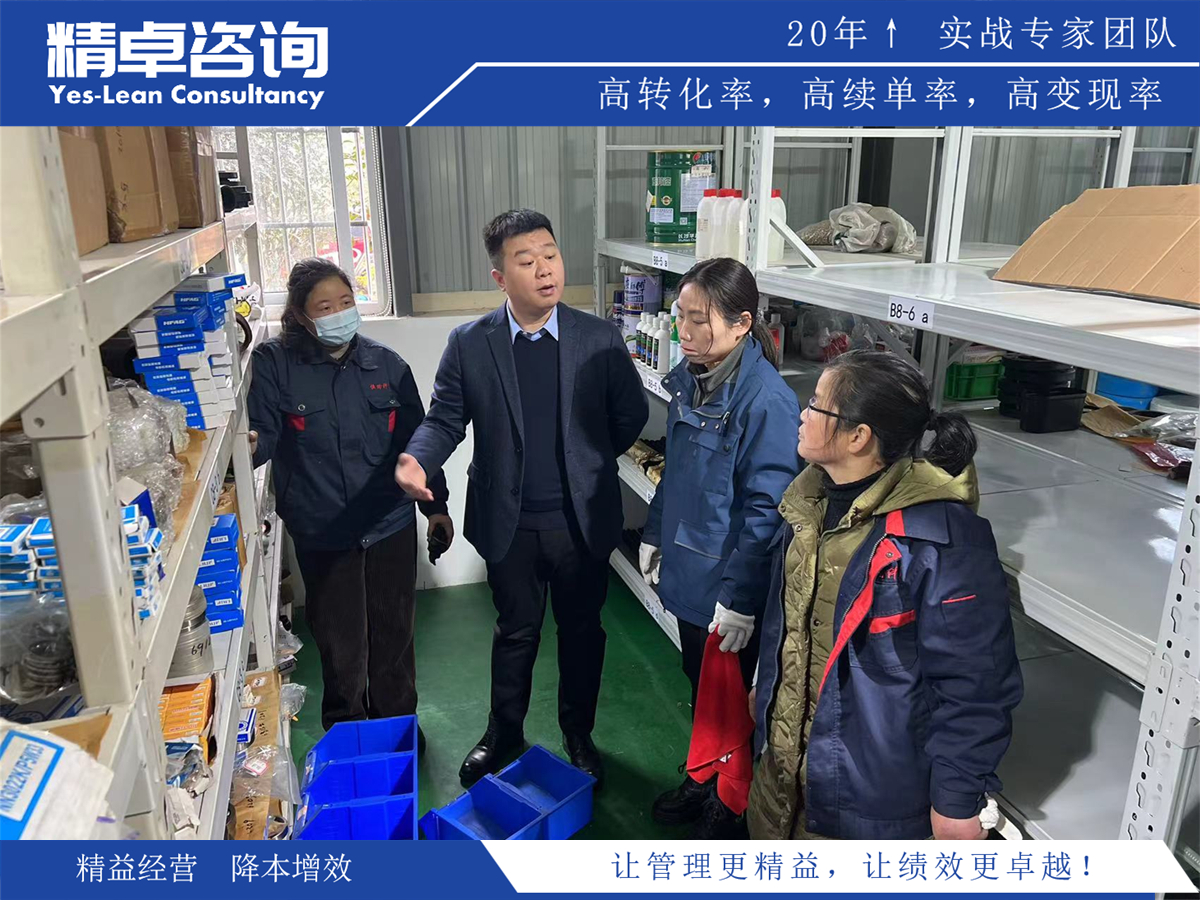
清扫阶段着重于保持纺丝车间的清洁和卫生,提高工作环境的舒适度。具体包括:
定期清洁地面、设备、工作台等,避免尘埃和杂物的积累。
清洁设备可以提高其性能,有助于维持产品质量。
4. Seiketsu(清洁):
清洁不仅仅是一次性的活动,还需要建立为日常习惯。这涉及:
制定清洁标准和规范,明确每个员工的责任。
培养员工的清洁自觉,使之成为日常工作中的一部分。
5. Shitsuke(素养):
素养阶段注重于维护和持续改进。这包括:
培训员工,让他们了解
5S管理制度的价值和意义。
建立反馈机制,鼓励员工提出改进意见,推动持续优化。
为什么仓储要实施5S管理
1、在物品管理方面:由于基建结束时间不长,仓库内堆积了大量的基建剩余物资,占用了仓库有限的空间,需要整理;随着机组生产投产运行,所需的各类生产物资的采购到货,由于种种原因,更加造成仓库内物资的无序放置,给仓储管理工作带来影响。
表现为物资乱堆放,物资没有标志,物资上有尘土,物品堆积过高,物品没有定位,无用的物品没有及时处理。无序的物资不仅增加了仓库工作难度,也给日常的仓储管理工作带来不便,不利于物资的保养和物资盘点工作。
2、在区域管理方面:区域划分相对混乱,仓库内没有划线标志,公共区域标志牌不合理,货架物资全部落实五五码放,四号定位的要求,随意放置等。
3、在工作环境方面:温度、湿度没有实行有效的监测,地面脏、乱、差,包装物随意乱放。
综上所述,纺丝车间可以通过
5S管理咨询方法优化生产流程,提高生产效率和产品品质。通过整理、整顿、清扫、清洁和素养五个步骤,创造一个整洁、有序、高效和安全的工作环境,为提升生产效能和员工士气提供有力支持。通过持续改进,纺丝车间可以不断提升自身的管理水平和绩效。