橡胶厂车间5S管理内容和标准,橡胶厂车间在橡胶制造过程中扮演着关键角色,负责橡胶的加工、成型和生产。为确保操作效率、产品质量和员工安全,实施有效的管理方法尤为关键。在橡胶厂车间中,应用5S管理方法可以优化工作环境、提高操作效率,并确保操作过程中的安全性。本文将深入探讨在橡胶厂车间中应用5S管理的核心内容、标准,以及它在维护产品质量和员工健康方面的作用。
企业5S管理的目标首先在于打造高效的工作环境。所谓高效,其内涵包括标准化、消除浪费、持续改善等多个层面的内容。但其zui基本的要求,就是建立不易做错的工作环境。
在5S管理推行之初,很多员工无法理解大量标识的作用,认为是画蛇添足。然而,正是基于这些简单的标识,任何一个新人都能快速融入环境,将物品放置在固定的位置,而不会随意乱放、造成混乱。
错误是造成企业浪费的重要原因:放错位置的物品,可能导致物品丢失;操作错误的员工,可能造成机器损坏。因此,工厂5S管理的首要目标,就在于借助各种看似“傻瓜”的细节,规避发生错误的可能。
橡胶厂车间5S管理简介
橡胶厂车间5S管理是一种基于整理、整顿、清扫、清洁和素养这五个步骤的管理方法,旨在创造整洁、有序、安全的工作环境,以提高操作效率、维护产品质量和员工安全。在橡胶制造过程中,确保操作无污染、无交叉感染至关重要,因此5S管理体系在橡胶厂车间具有特殊的意义。
1. 整理 (Seiri - 整理)
整理是橡胶厂车间5S管理的首要步骤。在这一阶段,需要识别并清除无关的物品、设备和工具,确保车间只保留与操作、产品质量和员工健康相关的物品。
2. 整顿 (Seiton - 整顿)
整顿的目标是有序地安排物品和设备,使操作人员能够迅速找到并使用所需的工具和材料。在橡胶厂车间中,整顿还涉及到规划合理的工作区域、存放物品的位置,以便员工高效操作。
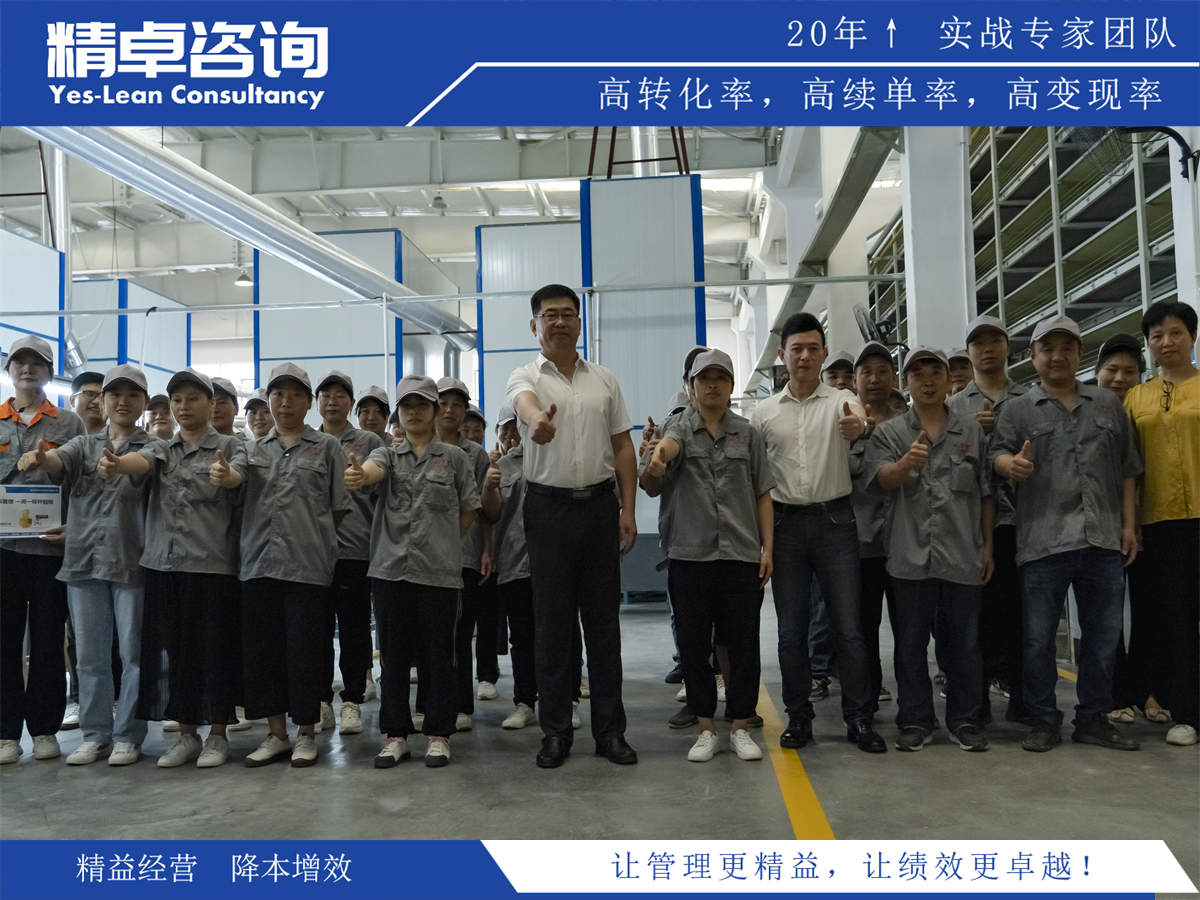
3. 清扫 (Seiso - 清扫)
清扫是维持橡胶厂车间的关键步骤。通过定期清理设备、工作台面、地面和周围区域,可以有效减少污垢、尘土和杂物的积累,保持洁净的操作环境。
4. 清洁 (Seiketsu - 清洁)
清洁阶段的目标是持续保持橡胶厂车间的清洁状态。制定清洁标准和规范,确保设备、工作台面、容器和工具保持清洁,降低交叉污染和污染风险。
5. 素养 (Shitsuke - 素养)
素养是将5S管理制度原则融入橡胶厂车间文化的过程。通过培养员工对清洁、安全操作和橡胶制造的责任感,使之成为日常操作的一部分,确保橡胶产品的质量和员工的安全。
橡胶厂车间5S管理的标准和优势
橡胶厂车间5S管理的标准旨在创造整洁、有序的工作环境,以提高操作效率、维护产品质量和员工安全。实施橡胶厂车间5S管理可以获得以下优势:
提高操作效率
橡胶厂车间5S管理可以优化物品和设备的存放位置,减少操作人员寻找物品的时间,提高操作效率,加速橡胶生产的流程。
维护产品质量
通过保持清洁、无尘的工作环境,橡胶厂车间5S管理有助于防止污染和杂质的引入,维护橡胶产品的高质量。
提升员工安全
橡胶厂车间5S标准化管理可以创造更安全的工作环境,减少员工因操作失误和杂物引发的安全风险,提升员工的安全意识。
保障产品质量
通过整顿和清洁,橡胶厂车间5S管理可以降低交叉污染风险,保障橡胶产品的质量。
实施橡胶厂车间5S管理的步骤
为了成功实施橡胶厂车间5S管理培训,企业应遵循以下步骤:
1. 制定计划
明确橡胶厂车间5S管理的实施计划,包括目标、时间表和责任分工。
2. 培训员工
为橡胶厂车间的员工提供关于5S管理的培训,传达其重要性和操作方法。
3. 整理工作区
与员工合作,识别并清除不必要的物品、设备和杂物,确保工作区域整洁、有序,降低操作失误风险。
4. 设定物品位置
为设备、工具、原材料等设定固定位置,以便员工可以快速找到并使用,提高操作效率。
5. 制定清洁流程
制定定期的清洁计划和程序,确保设备、工作台面、容器和工具保持清洁,降低交叉污染和污染风险。
6. 培养员工素养
通过鼓励员工定期清洁工作区、遵守操作规程和生产流程的规范,培养员工对产品质量和安全的责任感。
总结
橡胶厂车间5S管理咨询在维护产品质量和员工健康方面发挥着重要作用。通过实施整理、整顿、清扫、清洁和素养的管理方法,橡胶厂车间可以创造更加卫生、有序的工作环境,为橡胶制造业的可持续发展提供支持。