5S
精益生产现场管理的实施原则,5S精益生产现场管理的实施原则旨在确保工作区域的整洁、有序、高效。以下是实施5S的主要原则:
1.全员参与:
所有员工都应该参与5S实施,无论其职位如何。
创建一个团队,包括不同层级和部门的代表,一起制定和执行5S计划。
2.连续改进:
5S不是一次性任务,而是一个持续改进的过程。
定期审查和改进5S计划,确保它适应变化的需求。
3.标准化:
制定清晰、可操作的标准化程序和工作指南,以确保每个人都明白如何执行5S。
确保标准程序的一致性,并及时更新以反映zui佳实践。
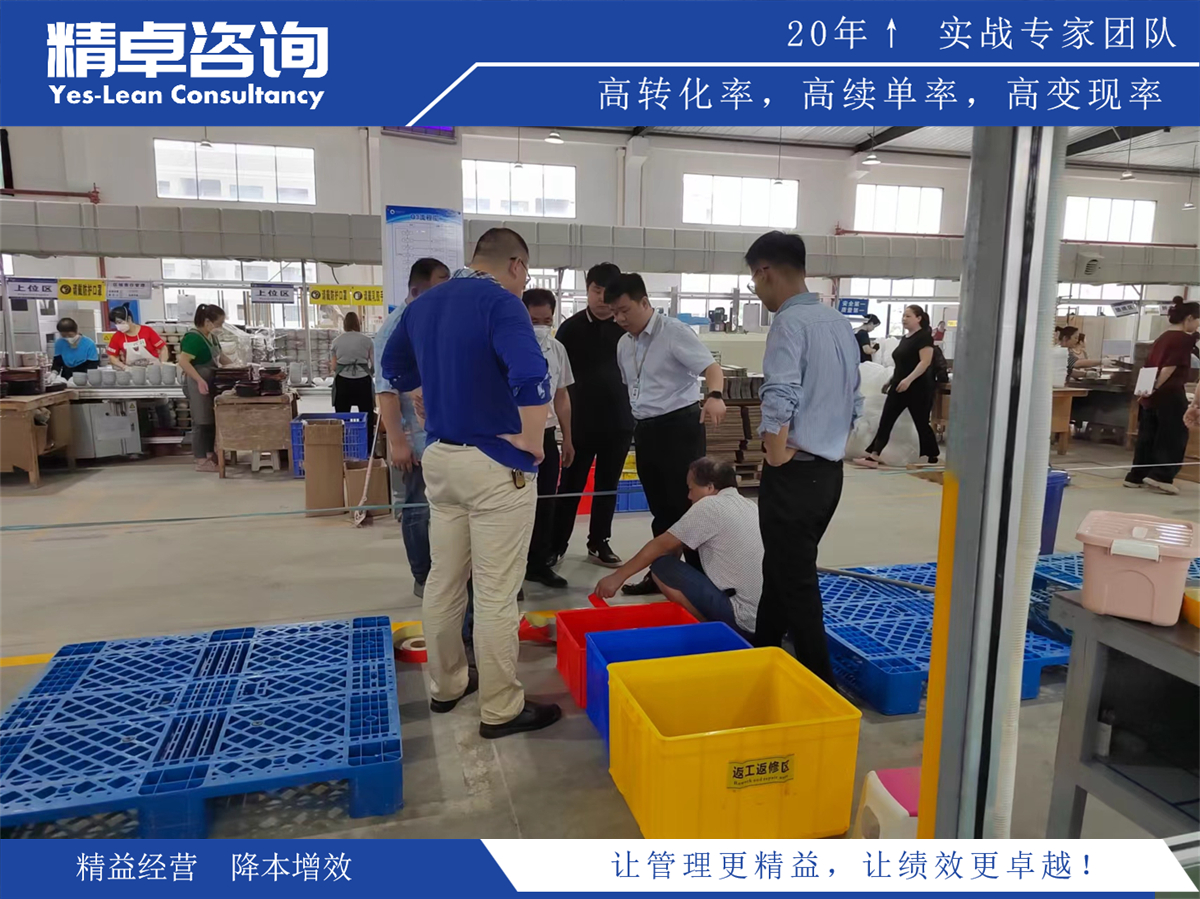
4.自我纠正:
培养员工的自我纠正习惯,他们应该能够立即识别和纠正问题。
鼓励员工报告任何5S违规或问题。
5.可视化:
使用标识、标签和视觉管理工具来使工作区域的状态一目了然。
帮助员工快速识别物品、设备和工具的位置。
6.教育和培训:
提供培训和教育,确保员工了解5S的原则和重要性。
培养员工的技能,以便他们可以有效地执行5S任务。
7.持续支持和奖励:
提供持续的支持和鼓励,以激发员工积极参与5S。
奖励和认可员工的卓越工作。
8.问题解决:
建立解决问题的机制,以便员工能够识别并解决引发混乱或浪费的问题。
鼓励员工提出改进建议,并快速响应这些建议。
9.逐步实施:
逐步引入5S原则,一次只关注一个S,确保每个S都充分实施和扎根。
不要贪多,首先专注于整理和整顿,然后再逐步推进清扫、清洁、素养和安全。
这些原则有助于确保5S的长期成功,并帮助组织建立一个高效、安全、干净和高素质的工作环境。不同的组织可能会根据其特定需求进行适度的定制和调整。