1.建立6S现场管理体系:
-Sort(整理):通过分类、清理工作场所,减少无用物品,优化工作环境,提高工作效率。
-Setinorder(整顿):设立标准化的工作流程和物品摆放位置,减少寻找时间,降低错误率。
-Shine(清扫):定期清洁工作场所,保持设备和环境清洁,提高生产效率和安全性。
-Standardize(标准化):制定标准化操作流程和作业规范,确保工作稳定性和一致性。
-Sustain(持续):培养良好的工作习惯和文化,持续推行6S管理,确保效果持久。
2.持续改进策略:
-PDCA循环:运用PDCA(Plan-Do-Check-Act)循环,持续评估和改进6S管理体系,不断优化工作流程和环境。
-Kaizen(改善)文化:培养改善文化,鼓励员工提出改进建议和创新想法,推动持续改进和创新。
-数据驱动决策:利用数据分析工具,监控关键绩效指标,发现问题瓶颈,制定有针对性的改进措施。
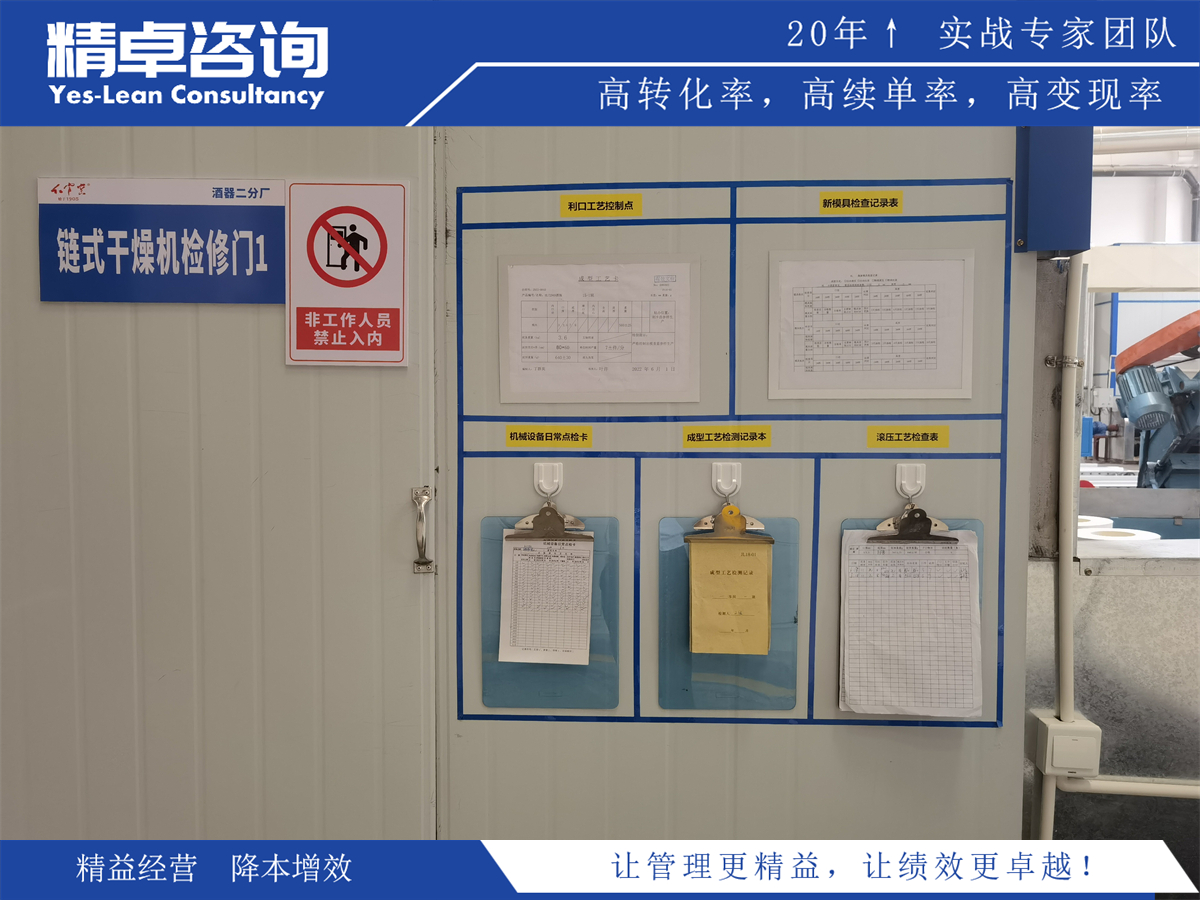
3.技术与数字化支持:
-智能化设备应用:引入智能化生产设备和工具,提升生产效率和质量,减少人为错误。
-数字化管理系统:建立数字化6S管理系统,实现对现场管理的实时监控和数据分析,提高管理效率和决策精准度。
4.员工参与与培训:
-全员参与:让所有员工参与到6S现场管理中,培养团队合作意识和责任心,共同提升生产效率。
-定期培训:提供定期的6S现场管理培训,加强员工对6S理念和方法的理解,提升执行力和质量意识。
5.持续监督与反馈机制:
-定期检查:建立定期的现场管理检查机制,发现问题和隐患,及时整改和改进。
-反馈机制:设立良好的反馈机制,鼓励员工提出问题和建议,促进沟通和改进,持续提升生产效率。
通过6S现场管理与持续改进策略的有效结合,企业可以实现生产效率的持续提升,打造高效、精益的生产环境,提升企业竞争力和持续发展能力。