本文将深入探讨5S生产现场管理方法及其效果评估指南。通过详细介绍5S的每个阶段如何实施,并提供有效的效果评估方法,帮助读者全面理解和应用
5S管理以提升生产现场的效率和质量。
5S生产现场管理方法
1.整理(Seiri)
-定义:分类整理工作场所,清除不必要的物品和杂物。
-步骤:
-确定工作区域和物品的使用频率和必要性。
-将不需要的物品移除或妥善处理。
-设定标准,标识哪些物品需要保留和丢弃。
2.整顿(Seiton)
-定义:优化物品摆放和工作区域布局,确保物品有序和便捷。
-步骤:
-设计优化的工作区布局,确保常用物品易于访问。
-标记和标识物品的存放位置,确保一目了然。
-建立定期检查机制,确保布局的持续有效性。
3.清扫(Seiso)
-定义:定期清洁工作场所,保持整洁和安全。
-步骤:
-制定清洁计划和标准,确保每日、每周或每月的清洁任务得到执行。
-培训员工清洁操作标准和方法,并监督执行情况。
-持续改进清洁流程和标准,确保适应变化的工作环境。
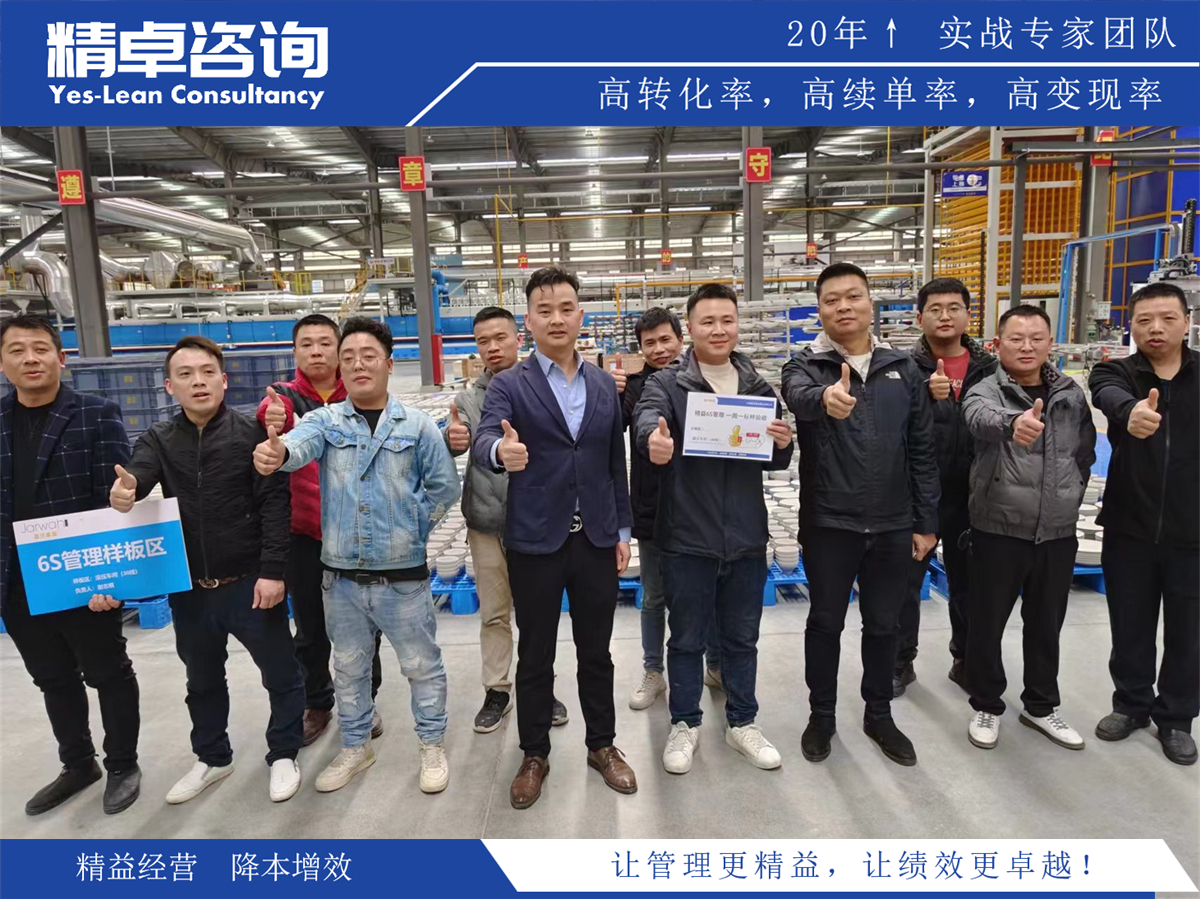
4.清洁(Seiketsu)
-定义:建立清洁标准和规范,确保持续执行。
-步骤:
-制定清洁标准文件,详细描述每个区域和设备的清洁要求。
-培训员工遵守和贯彻清洁标准,确保一致性和持续性。
-定期检查和评估清洁标准的执行情况,并作出必要的调整和改进。
5.素养(Shitsuke)
-定义:培养员工遵守和贯彻
5S标准的习惯和文化。
-步骤:
-建立培训计划,教育员工5S管理的重要性和技能。
-激励和表彰积极参与和创新的员工,促进组织文化的改进。
-定期进行回顾和评估,确保5S文化的长期建立和持续改进。
效果评估指南
1.定量指标
-生产效率:比如产量提升、生产周期缩短。
-缺陷率:产品质量改善是否导致缺陷率降低。
-工作安全:事故率是否下降。
2.定性指标
-员工参与度:员工对5S管理的积极态度和参与度。
-工作环境:工作场所的整洁度和有序度改善情况。
-管理效率:管理层对5S执行的支持程度和效果。
3.评估周期
-短期评估:每月或每季度评估5S的初步效果。
-长期评估:每年一次的全面评估,检查5S文化的持续性和改进潜力。
结论
通过以上方法和指南,可以有效实施和评估5S生产现场管理,提升工作效率、质量和员工满意度。关键在于持续的培训、管理支持和定期的评估反馈机制,确保5S管理的长期成功和持续改进。