6S管理法是一种致力于改善工作环境、提高效率和安全性的管理方法,它包括整理(Sort)、整顿(Setinorder)、清扫(Shine)、标准化(Standardize)、持续改进(Sustain)和安全(Safety)这六项原则。现代化工厂在实施6S管理过程中,通过这些原则提高生产效率、降低成本、增强安全意识,并持续改进工作流程。以下是在现代化工厂中的6S管理应用实例:
1.整理(Sort)
在工厂生产线上,员工可以根据工作需要清理工作区域,移除多余的工具、材料和设备,使工作区更加整洁和有序。例如,通过分类、标记和处理不必要的物品,减少浪费和提高操作效率。
2.整顿(Setinorder)
工厂可以优化工作站和生产线布局,将工具、物料和零件有序地摆放,确保员工能够轻松获得所需物品而不耽误生产时间。例如,为每个工具和零件设置指定的存放位置,并使用标示标识,加快查找速度。
3.清扫(Shine)
保持工作区域的清洁是关键的一环。定期清理设备、地面和生产线,防止积尘和脏污影响生产质量和工作效率。例如,清洁设备表面、地板和墙壁,确保生产环境整洁。
4.标准化(Standardize)
制定操作流程、标准作业程序和工作规范,确保员工遵守相同的工作标准,减少错误和提高生产一致性。例如,制定设备操作指南,培训员工按照规范操作设备。
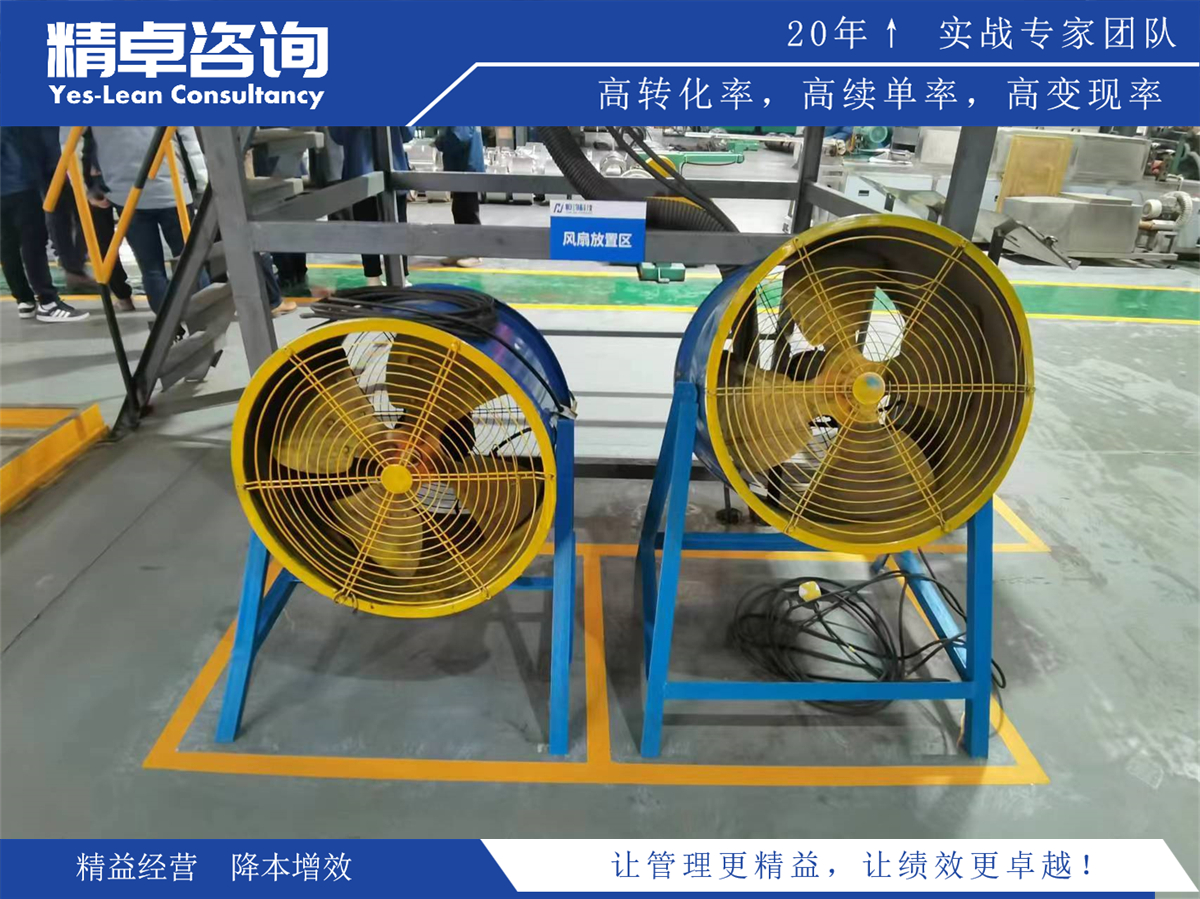
5.持续改进(Sustain)
建立持续改进的文化,鼓励员工提出改进建议,解决问题并优化工作流程。例如,定期召开改进会议、收集反馈意见并实施改进计划,持续提升生产效率和质量水平。
6.安全(Safety)
将安全作为首要任务,加强安全意识培训、建立安全管理制度,确保生产过程中的安全。例如,制定安全操作程序、提供个人防护装备、进行定期安全培训,降低事故风险。
应用实例:
在一家汽车零部件制造工厂中,实施了
6S管理法。他们通过整理工作区域,清除多余的工具和原料;整顿工作站布局,合理摆放零部件和设备;定期清扫生产线,保持清洁;制定标准作业程序,规范员工操作;持续改进工作流程,提高生产效率;加强安全意识,提供安全培训和设备。这些措施使工厂生产效率提升、产品质量提高,并减少了工作事故的发生。
通过引入6S管理法,现代化工厂可以全面提升生产效率、产品质量和员工安全意识,推动工作流程的持续改进,实现生产环境的规范化和最优化。