车间
5S管理是
精益生产中的重要组成部分,旨在通过“整理、整顿、清扫、清洁、标准化”五个步骤,改善工作环境、提高生产效率、减少浪费,从而提升生产线整体质量。通过实施5S管理,车间不仅能提高生产效率,还能确保产品质量稳定,降低安全事故的发生,进一步增强企业的竞争力。以下是如何利用车间5S来提高生产线整体质量的详细分析:
一、5S管理的核心内容与目标
1.整理(Sort):清理车间内的杂物,确保只有必要的工具、设备和原材料留下。
2.整顿(SetinOrder):对剩余物品进行合理摆放,确保工具和设备易于找到且易于使用。
3.清扫(Shine):保持车间环境整洁,包括工具、设备、工作区域的清洁,确保生产设施处于良好状态。
4.清洁(Standardize):制定清洁标准,确保各项工作都按计划和标准执行,避免出现“懒散”或不一致的情况。
5.素养(Sustain):培养员工的5S意识和行为习惯,将
5S管理制度化、常态化,确保其长效执行。
通过这五个步骤,车间管理可以变得更加规范、流程更加高效,从而有效提升生产线的质量。
二、车间5S如何提升生产线整体质量
1.减少浪费,提升生产效率
-整理:通过清理车间不必要的工具、物料和设备,消除浪费,减少寻找工具和材料的时间。生产人员不再被无关物品干扰,可以集中精力工作,减少了无效操作和等待时间。
-整顿:优化生产环境中的物料存放与工具摆放,确保生产人员能快速找到所需工具或材料。明确的工作区域和流程有助于减少因物品混乱导致的生产停滞,避免出现生产中断或错误。
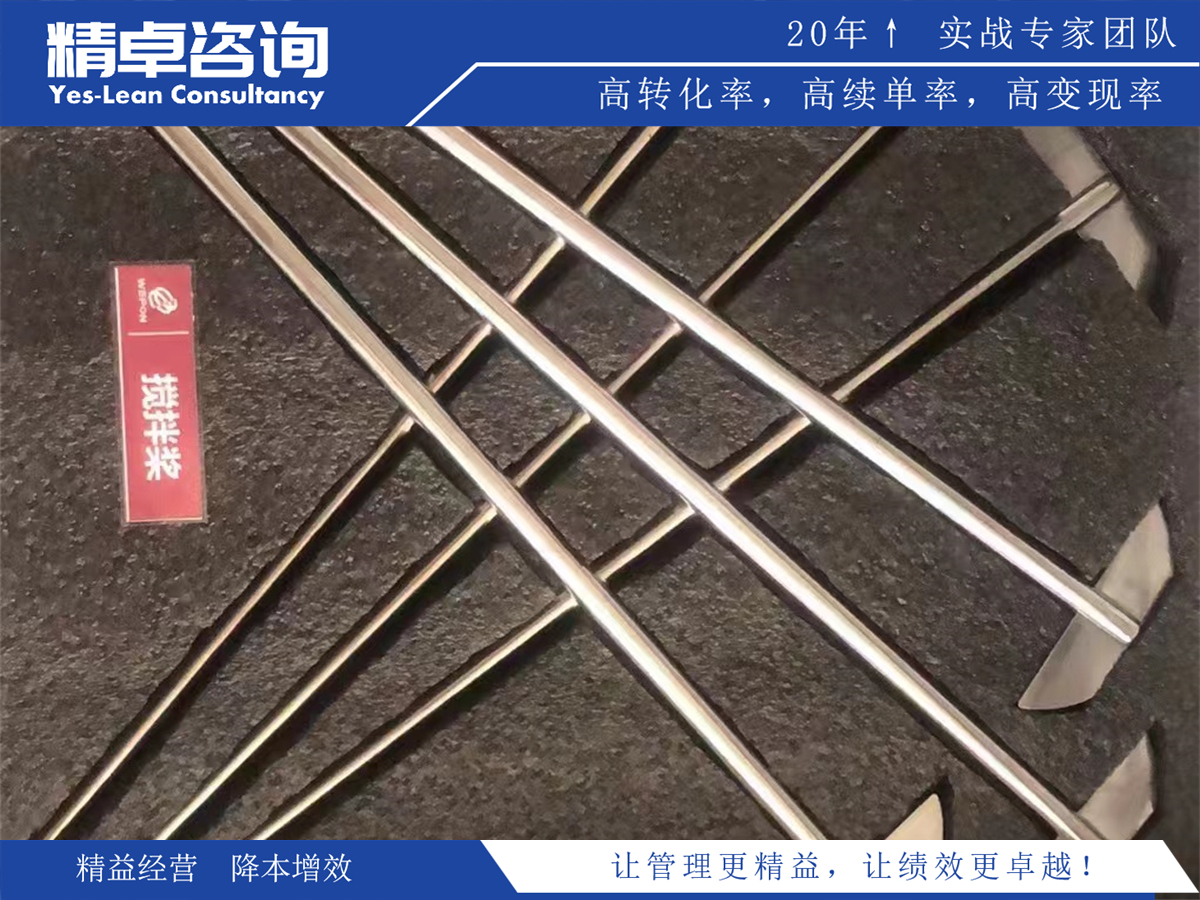
2.减少缺陷,提升产品质量
-清扫与清洁:定期清洁生产设备和工具,确保设备处于良好的工作状态。清洁的生产环境减少了设备故障的概率,提升了设备的精准度,避免因设备污染或设备故障导致的产品质量问题。生产线上清洁无杂物的工作环境也能减少人为错误,降低操作失误的发生率。
-标准化:通过制定明确的操作标准,确保每个员工按照统一的操作流程进行工作。这不仅能提高生产的一致性和可控性,还能减少生产过程中出现的偏差和质量波动。
3.提高安全性,减少事故率
-整顿和清洁:通过合理的工具和物料摆放,确保车间内的通道和工作区无阻碍物。清洁工作可以避免地面上散落的工具或物料造成的绊倒或滑倒事故,从而降低安全隐患。安全的工作环境能够减少工伤事故的发生,保证生产线持续平稳运行。
-素养化:培养员工的安全意识和5S意识,确保每个员工都能主动识别潜在的安全隐患,并及时报告和改进。员工对5S管理的参与感和责任感增强,能更好地保障生产安全,减少因人为操作失误导致的事故。
4.提高员工工作满意度
-整顿与清扫:通过清理工作区和工具的合理摆放,员工能够在整洁有序的环境中工作,这不仅提升了他们的工作效率,也能提高员工的工作满意度和归属感。
-素养化:通过定期培训和5S文化的推广,员工对5S管理的理解和执行力不断提高,增强了他们对生产质量和安全的责任心。这样不仅能提升员工的整体工作表现,还能促进团队协作。
5.支持持续改进,优化生产流程
-标准化:5S管理中的标准化不仅限于清洁和整顿,还包括生产流程的标准化。通过标准操作流程(SOP)的制定,车间内的工作步骤、工具使用、物料管理等都会有清晰的规定。这使得生产线的各项环节更加精确、规范,有助于减少偏差和变异,提升产品的稳定性和一致性。
-素养化:培养员工主动参与改进的意识,持续推进5S的优化。例如,通过员工提出的合理化建议,改进工作流程和生产环境,进一步提升整体生产效率和质量。
三、车间5S管理的评估与持续改进
1.定期检查与评估:通过定期的5S检查,评估车间的5S执行情况,找出存在的问题并提出改进措施。可以通过内部审查、第三方评估或员工反馈等多种方式进行。
2.持续改进机制:建立持续改进的机制,通过PDCA(计划-执行-检查-改进)循环,不断优化车间5S管理的各个环节。例如,通过数据分析找出浪费环节,并及时调整生产流程或工作标准。
3.员工参与与激励:5S的实施需要全员参与,鼓励员工在日常工作中提出问题并提出改进意见。同时,设立奖惩机制,对执行良好的员工进行表彰,激励员工积极参与到生产质量的提升中。
四、总结
车间5S管理不仅仅是一个简单的环境管理工具,它涵盖了生产线各个环节的优化和改进。通过实施5S管理,企业可以有效地减少浪费、提高生产效率、保障产品质量和安全、提升员工满意度,最终提高生产线的整体质量。通过不断的评估与持续改进,5S管理能够为企业提供一个持续优化的机制,使企业能够在竞争激烈的市场中保持优势。
因此,企业应将车间5S管理作为提高生产线质量的长期战略,积极推动其在生产线中的深入实施,确保其可持续性并最终带来显著的效益。