5S管理作为
精益生产的一项基础性工具,已被广泛应用于制造业和生产车间。通过“整理、整顿、清扫、清洁、标准化”五大要素,5S管理帮助企业提高了生产效率、减少了浪费、提升了工作环境的安全性。然而,在实际实施过程中,许多企业面临着种种挑战和难题,影响了5S管理效果的发挥。本文将深入探讨
车间5S管理制度实施中的常见问题,并提出有效的解决方案。
一、常见问题一:员工参与度不足
在实施5S管理过程中,员工的参与度往往是成功与否的关键。然而,很多车间员工并未完全理解5S的意义,或缺乏足够的参与意愿,导致5S管理流于形式,无法达到预期效果。
解决方案:
1.加强培训与宣传:通过定期的培训和宣传活动,让员工了解5S管理的核心理念和其对提高工作效率、安全性及环境整洁的积极作用。培训不仅要涵盖理论知识,还应通过案例分析、现场演示等方式帮助员工掌握具体的操作技能。
2.提升员工的自我管理意识:通过设置激励机制,如评选“5S优秀员工”或“清洁先锋”,鼓励员工主动参与5S管理。还可以将5S管理成绩纳入员工绩效考核,增强员工的责任感和积极性。
3.领导带头示范:管理层应积极参与5S活动,并通过身先士卒的方式,树立榜样。管理层的重视和参与能够激励员工主动投入到5S管理中。
二、常见问题二:标准化实施不到位
标准化是5S管理的核心环节之一,其目的是通过制定明确的操作标准,确保5S管理长期有效。然而,很多车间在实施标准化操作时,由于缺乏规范和持续的监督,导致标准化管理效果难以落实。
解决方案:
1.制定详细的标准化流程:企业应根据车间的实际情况,制定详细且易于执行的
5S标准化操作流程,明确每一项任务的责任人、操作步骤及检查标准。
2.加强监督与反馈机制:建立完善的监督机制,通过定期检查、评审和员工反馈,确保5S标准得以有效执行。检查人员应具备专业素养,能够发现潜在的问题并及时提出整改措施。
3.持续改进:标准化操作不是一成不变的,企业应定期对实施效果进行评估,及时修订和完善5S操作标准,以适应生产过程的变化和新需求。
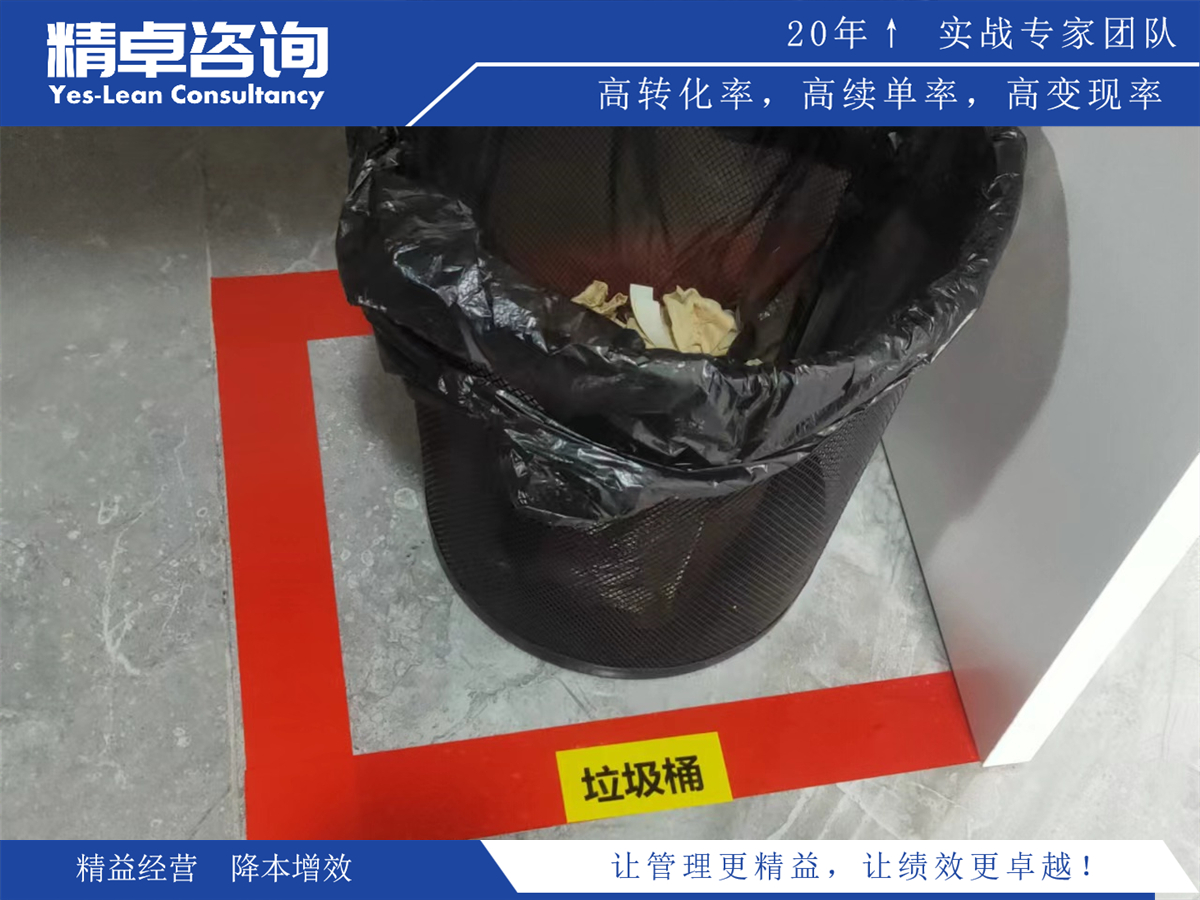
三、常见问题三:资源不足或投入不够
5S管理的顺利实施需要企业投入一定的资源,尤其是在设备、工具和培训方面。然而,很多企业在初期实施5S管理时,未能充分投入资源,导致5S管理无法有效落地。
解决方案:
1.高层管理支持与资源保障:管理层应充分认识到5S管理的重要性,并为其提供必要的资金、人员和设备支持。企业可以通过将5S管理纳入长期战略规划来保障资源的持续投入。
2.合理规划资源分配:在资源配置方面,应根据车间实际情况优先保证关键领域的资源投入,如清扫工具、设备维修工具及员工培训资源等。
3.逐步实施与改进:在资源有限的情况下,企业可以采取分阶段、逐步推进的方式实施5S管理。从最基础的整理和整顿做起,逐步完善其他环节。随着效果的显现,资源的投入可以逐步增加。
四、常见问题四:缺乏持续性和执行力度
5S管理是一个长期的过程,需要不断的跟进和改进。然而,许多企业在初期推动5S管理时取得了一定的效果,但随着时间推移,管理力度逐渐减弱,导致5S管理的执行力大打折扣。
解决方案:
1.定期检查与评估:定期对5S管理进行效果评估,检视各项措施是否得到贯彻和落实。如果发现存在执行不力的现象,应及时调整策略和方法。
2.建立持续改进机制:企业应根据车间实际的生产变化,不断优化和改进5S管理的实施方式。鼓励员工提出改善意见,并针对这些建议进行评估和采纳。
3.建立持续激励机制:通过建立持续的激励机制,保持员工对5S管理的热情。例如,定期评选“5S最佳车间”或“5S明星员工”,并给予物质奖励或荣誉奖。
五、常见问题五:清扫和清洁工作不到位
清扫和清洁工作是5S管理的重要组成部分,它涉及到车间环境的整洁和设备的维护保养。然而,在许多企业中,清扫和清洁工作往往因工作量大、工人分心等原因而落实不力,导致车间环境脏乱差,设备故障率高。
解决方案:
1.制定清扫与清洁责任制:为每个车间区域和设备制定明确的清扫与清洁责任人,确保责任到人。定期检查清洁工作是否到位,并对未完成的任务进行整改。
2.实施设备日常维护计划:除了常规的清扫工作外,还应制定设备的定期维护计划,确保设备在正常状态下运行。通过预防性维护,避免设备故障影响生产。
3.加强员工培训:培训员工掌握正确的清扫技巧和清洁方法,避免盲目清洁导致设备损坏或资源浪费。
六、常见问题六:对5S文化缺乏认同感
5S管理不仅仅是一个操作系统,它更是一种企业文化的体现。如果企业未能营造起一个全员参与、共同遵守的5S文化氛围,单靠管理层强制执行,效果也会大打折扣。
解决方案:
1.推动5S文化建设:通过各种方式强化5S文化的传播,提升全员对5S管理的认同感。通过海报、宣传板、定期交流会等方式,向员工传递5S管理的意义和价值。
2.领导示范作用:管理层应以身作则,带头实施5S管理,增强员工对5S文化的认同和尊重。领导层的行为会潜移默化地影响员工,使5S管理成为企业文化的一部分。
3.建立员工反馈机制:通过员工座谈会、匿名调查等形式,及时了解员工对5S管理的看法和建议,调整实施策略和管理方式。
结语
车间5S管理制度的实施虽面临诸多挑战,但通过系统化的管理和持续改进,完全可以克服这些困难。企业在实施5S管理时,应充分认识到员工参与、标准化操作、资源保障和文化建设等方面的重要性,采取科学的管理方法,不断调整和优化实施细节。只有这样,5S管理才能真正为企业创造出更高的生产效率、产品质量和工作环境,从而推动企业向精益生产的目标迈进。