精益生产合理化建议和措施,精益生产合理化建议和措施主要涉及到以下几个方面:
1. 价值流分析:
- 进行价值流分析,了解整个生产过程中的价值流动情况,明确价值创造的环节和存在的浪费,为后续的优化提供基础。
2. 流程优化:
- 优化生产流程,消除不必要的环节和瓶颈,确保生产过程更为顺畅,提高生产效率。
3. 单分钟交换模具(SMED):
- 实施SMED,减少设备切换时间,提高设备利用率,支持灵活生产和多品种生产。
4.
5S管理:
- 推行5S管理,通过整理、整顿、清扫、清洁和素养等手段,创造整洁有序的工作环境,提高工作效率。
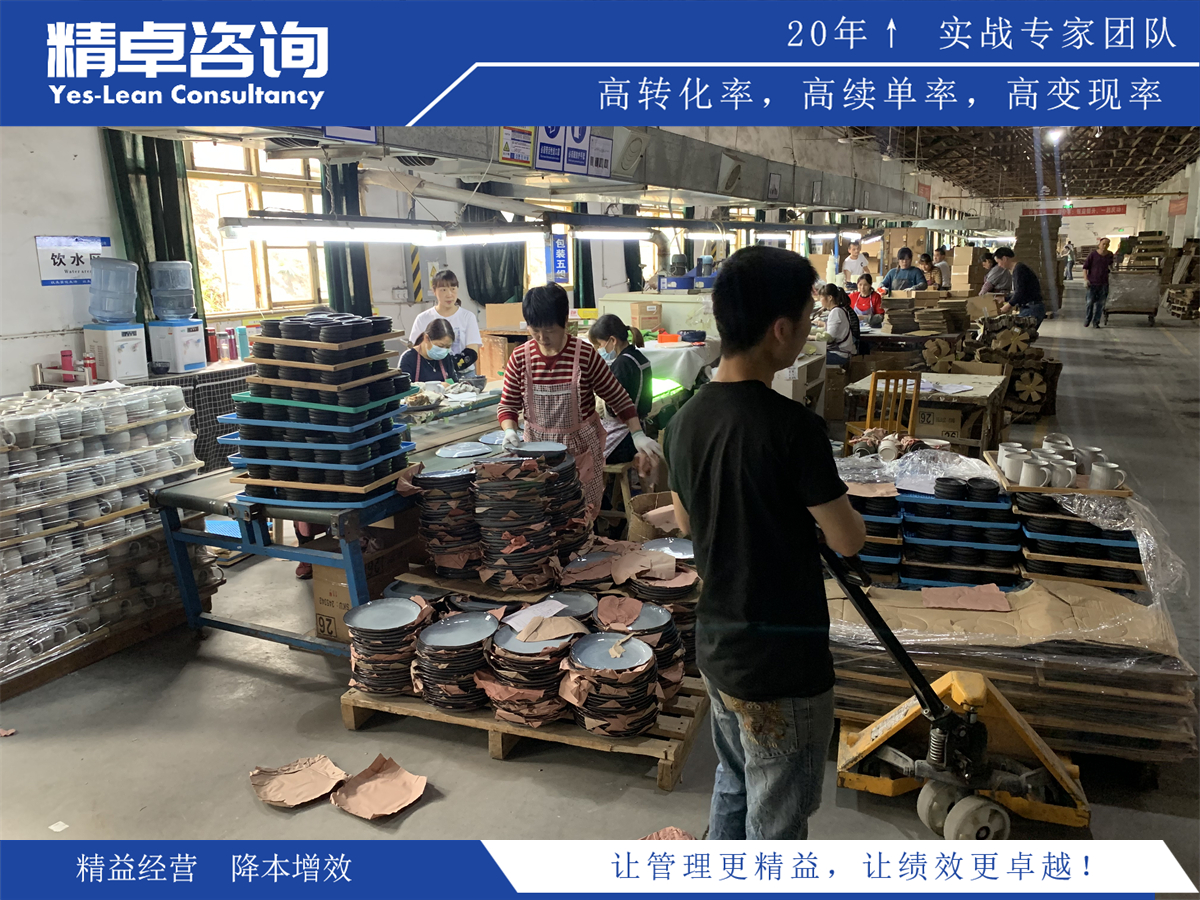
5. 可视化管理:
- 使用可视化管理工具,如看板、生产监控系统等,使生产状态、进度等信息对所有相关人员可见,提高沟通效率。
6. 员工培训和参与:
- 进行员工培训,提高员工技能水平,鼓励员工参与流程改进,形成全员参与的良好氛围。
7. 标准化工作:
- 制定和遵循标准工作程序,确保操作一致性,降低变异性,提高质量稳定性。
8. 持续改进(Kaizen):
- 建立持续改进的机制,鼓励员工提出改进意见,进行小步快跑的改进,不断追求卓越。
9. 质量控制和防错:
- 强调质量控制,采用先进的质量管理方法,通过防错和纠错手段,确保产品质量符合标准。
10. 供应链协同:
- 与供应商和合作伙伴建立紧密的合作关系,优化整个供应链,确保物料供应的及时性和稳定性。
11. 灵活生产:
- 提高生产线灵活性,使其更容易适应市场需求的变化,降低生产调整的成本。
12. 设备维护管理:
- 实施定期维护和预防性维护,确保设备处于良好状态,减少生产中断和损坏的风险。
这些建议和措施可以根据企业的具体情况和需求进行调整和定制,帮助企业实现生产合理化,提高生产效益和竞争力。