在
精益生产中,消除浪费是提升效率和降低成本的核心目标。本文将探讨精益生产中识别和消除浪费的有效方法,并通过实践案例展示这些方法的成功应用,帮助企业实现更高的运营效率和更低的生产成本。
一、精益生产中的浪费类型
根据精益生产理论,浪费主要分为以下七种类型:
1. 过度生产:
- 生产超过需求的产品。
2. 等待:
- 由于生产流程不顺畅导致的等待时间。
3. 运输:
- 不必要的物料运输和移动。
4. 库存:
- 过多的原材料、在制品或成品库存。
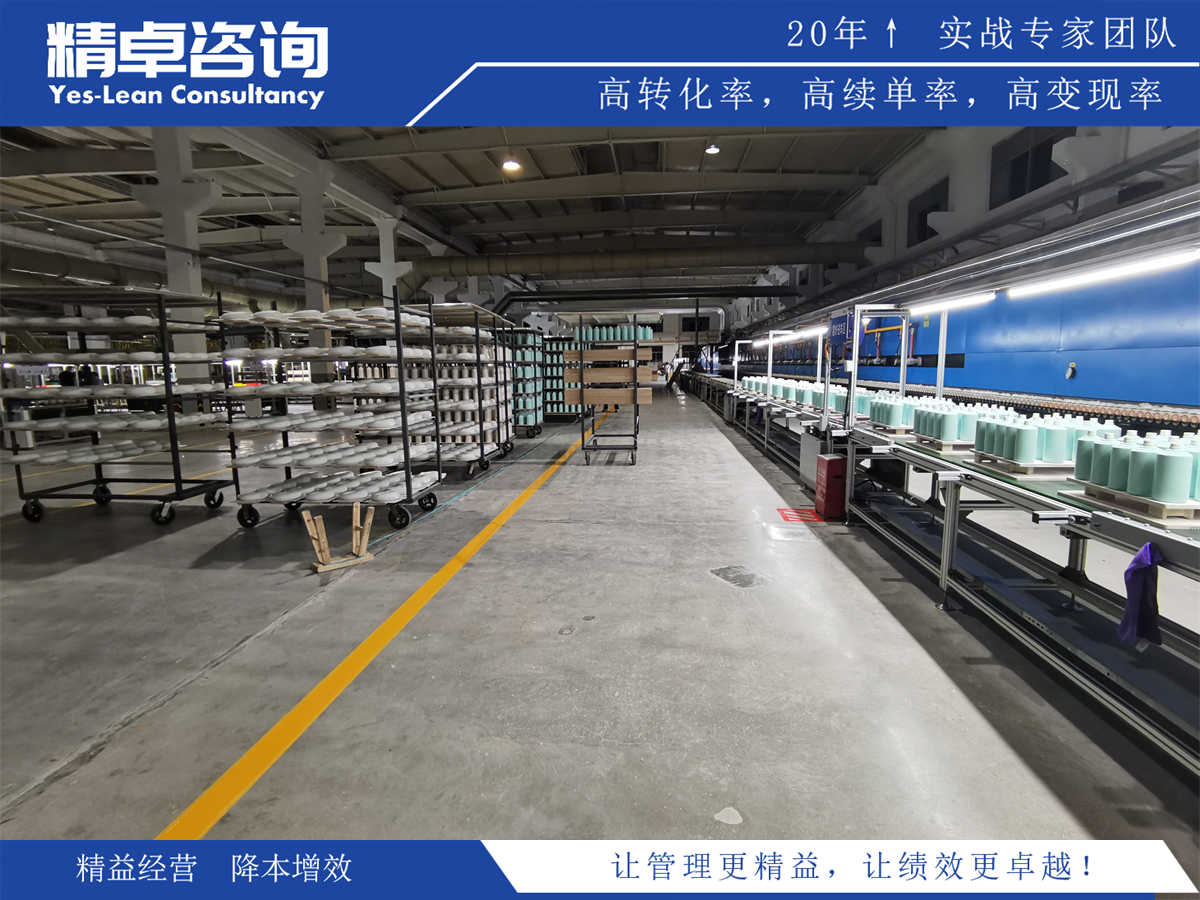
5. 运动:
- 不必要的人体动作,如寻找工具或材料。
6. 缺陷:
- 不合格产品的产生,导致重工或报废。
7. 过度加工:
- 产品加工超过客户需求的要求。
二、消除浪费的有效方法
1. 价值流图(VSM):
- 通过绘制现有流程图,识别每一步的增值和非增值活动,找出浪费点并制定改进计划。
2.
5S管理:
- 实施整理、整顿、清扫、清洁和素养五个步骤,创建高效、整洁的工作环境,减少寻找工具和材料的时间。
3. 看板系统:
- 利用看板系统进行可视化管理,控制生产和库存水平,避免过度生产和库存积压。
4. 单件流(One-Piece Flow):
- 采用单件流的生产方式,减少工序间的等待时间,提高效率。
5. 持续改进(Kaizen):
- 鼓励员工提出改进建议,定期进行小规模的改进活动,逐步消除浪费。
三、实践案例
案例:某汽车零部件制造厂
背景:
该制造厂面临生产效率低和库存过高的问题,决定实施精益生产来消除浪费。
实施步骤:
1. 价值流图绘制:
- 通过分析现有生产流程,识别出多个浪费点,特别是等待时间和库存积压。
2. 实施5S:
- 进行全面的5S活动,确保工作区域整洁有序,减少员工寻找工具的时间。
3. 引入看板系统:
- 设置看板,确保生产过程中物料和产品的实时可视化管理。
4. 单件流试点:
- 在一个生产线进行单件流试点,缩短了工序间的等待时间。
效果:
- 生产效率提高了30%,库存减少了40%,客户满意度显著提升。
四、总结
消除浪费是精益生产的核心任务,通过实施有效的方法,如价值流图、5S管理和看板系统,企业可以显著提升生产效率并降低成本。通过实际案例的分析,企业能够看到精益生产方法在实践中的成功应用,进一步推动持续改进与创新,实现卓越运营。