现场目视化管理是提高生产效率、降低错误率、优化流程的重要手段之一。通过可视化信息展示,员工能够更直观地了解生产状态、任务进度和质量要求。本文将讨论提升生产效率的现场目视化管理的实施策略,并结合案例进行分析。
1.实施策略
1.1确定关键指标
首先,确定需要展示的关键生产指标,如生产进度、质量数据、设备运行状态等。这些指标应能反映生产过程的关键环节,并与整体生产效率紧密相关。
1.2设计可视化展示物
选择合适的可视化展示物,如生产看板、数据面板、实时监控屏幕等。这些展示物应该能够清晰地呈现关键指标,同时便于员工快速理解和获取信息。
1.3制定标准化标识和视觉管理规范
为生产现场的设备、区域、物料等制定标准化的标识和视觉管理规范,如颜色编码、形状标识等。这有助于员工快速识别、理解和遵循相关规定。
1.4培训和沟通
为员工提供相关的目视化管理培训,让他们了解目视化管理的重要性、展示物的含义和使用方法。同时,建立定期沟通机制,让员工分享使用目视化管理的体会和建议。
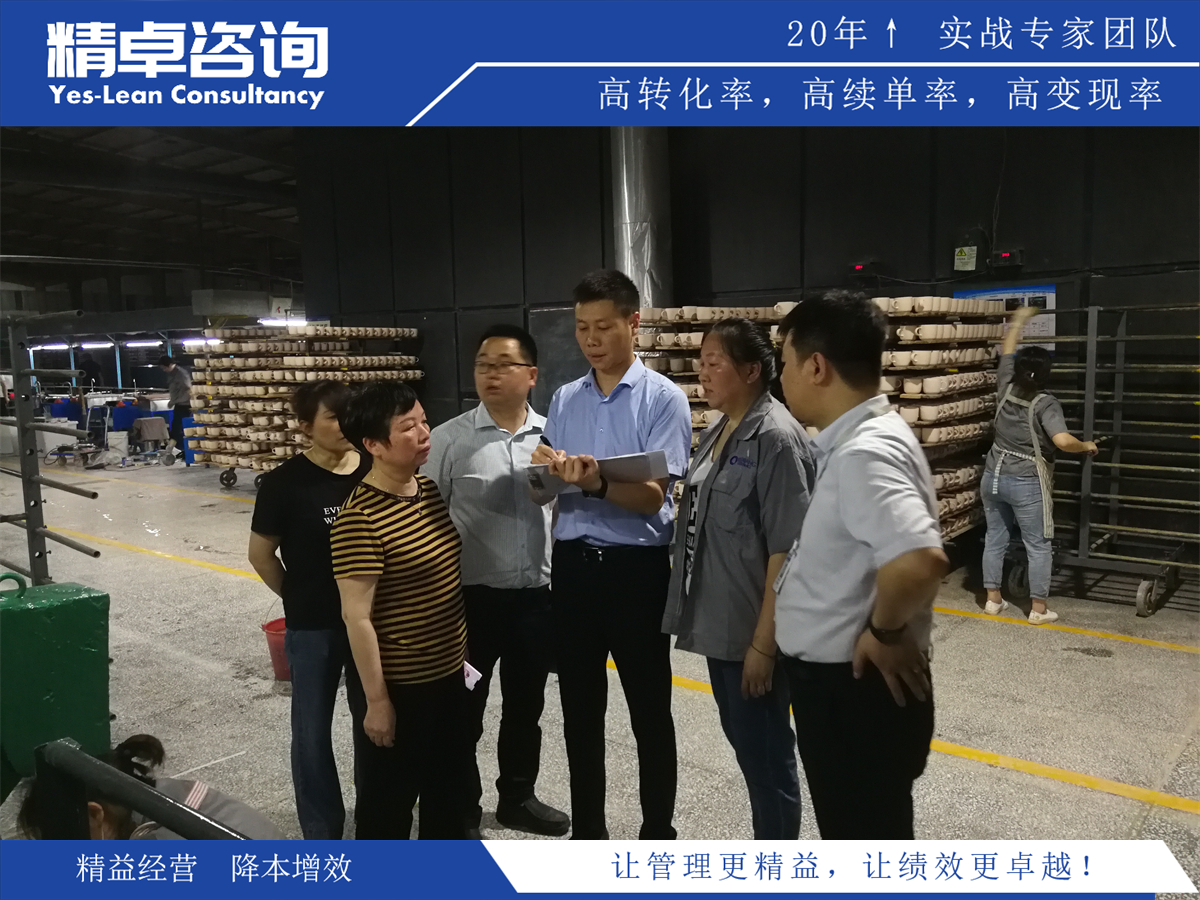
1.5持续改进和优化
目视化管理不是一次性的工作,而是需要持续改进和优化的过程。定期评估可视化展示效果,收集反馈意见,及时对展示物进行调整和优化。
2.案例分析:Toyota的Andon系统
Toyota作为
精益生产的代表企业之一,其Andon系统是现场目视化管理的典范。Andon系统通过安装在生产线上的灯光、屏幕或声音设备,快速传递生产信息,让每个人都了解生产状态。
2.1实施策略
-关键指标:Toyota的Andon系统展示了生产线的生产进度、异常信息、质量问题等关键指标。
-可视化展示物:使用了易于理解的灯光、屏幕等展示物,直观显示了生产状态和异常情况。
-标识和规范:生产线上采用了统一的标识和规范,如颜色编码表示不同类型的问题,让员工迅速识别和处理异常。
-培训与沟通:Toyota对员工进行了Andon系统的培训,建立了团队间的紧密沟通机制,鼓励员工主动参与问题解决和改进。
2.2效果分析
通过Andon系统,Toyota实现了以下效果:
-实时响应:生产现场出现问题时,通过Andon系统能够立即通知相关人员,加快问题解决速度。
-员工参与:员工更加积极参与生产过程,通过Andon系统和其他可视化管理工具了解生产状态,主动发现并解决问题。
-持续改进:Andon系统的使用促进了持续改进的文化,员工对生产中的问题提出建议,不断完善生产管理。
结论
通过以上案例分析,我们可以看到,现场目视化管理对提升生产效率和质量至关重要。以上实施策略和案例为企业提升生产效率的目视化管理提供了有益的参考,希望能有效地帮助企业提升生产效率。