优化生产过程的精益车间现场管理实践,精益车间现场管理是一种旨在优化生产过程和提高效益的管理方法。它强调通过消除浪费、提高质量和增强员工参与来实现持续改进。下面将介绍优化生产过程的精益车间现场管理实践。
1. 价值流分析
价值流分析是精益车间现场管理的核心工具之一。通过绘制产品或服务的价值流程图,识别出价值增加和非增加的环节,从而找出产生浪费的根源。在价值流分析的基础上,制定改进计划,通过精细化的流程优化,实现生产过程的高效运作。
2. 5S 实施
5S 是精益车间现场管理的基础步骤之一。通过整理、整顿、清扫、清洁和素养五个步骤,创造一个干净、有序、高效的工作环境。5S 实施可以减少搜寻时间,提高工作效率,降低事故风险,改善工作氛围,为
精益生产奠定良好的基础。
3. 小批量生产
小批量生产是精益车间现场管理的重要原则之一。通过减少批量生产的规模,缩短交付周期,降低库存水平,可以更快地响应市场需求变化。小批量生产可以减少存货积压和过剩生产,提高生产灵活性和响应速度。
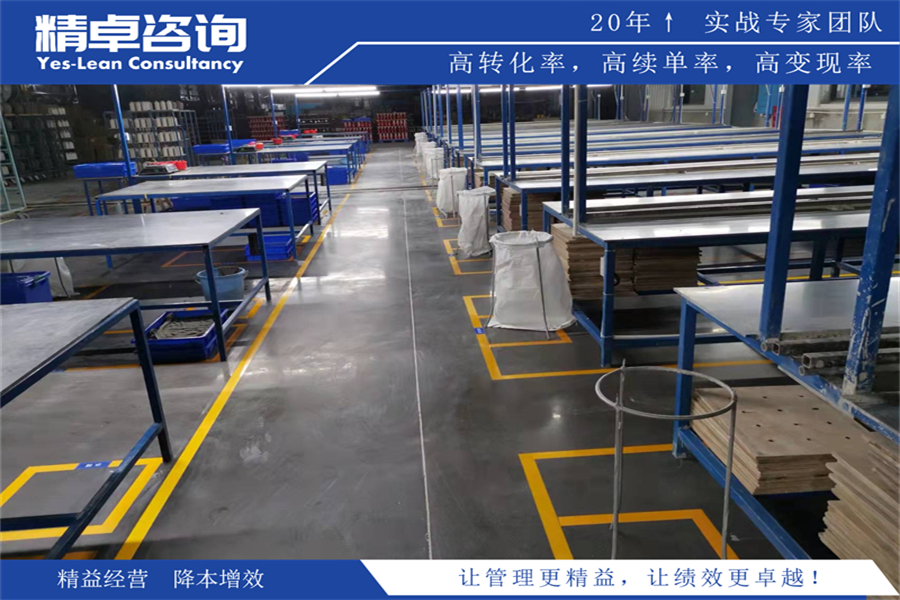
4. 持续改进
持续改进是精益车间现场管理的核心理念之一。通过设立改进目标、收集数据、分析问题、制定改进措施和持续监控,不断追求生产过程的优化和提升。通过员工的参与和团队合作,推动持续改进文化的建立,实现生产过程的不断演进和创新。
5. 质量控制和自动化
精益车间现场管理强调质量的重要性。通过建立严格的质量控制体系,制定工艺标准和操作规范,确保产品质量的稳定性和一致性。同时,引入自动化设备和技术,提高生产过程的精度和效率,减少人为因素的干预,降低质量风险。
优化生产过程的精益车间现场管理实践通过价值流分析、5S 实施、小批量生产、持续改进以及质量控制和自动化等方法,实现生产过程的精益化和高效化。它注重消除浪费、提高质量和优化流程,促进生产效益的持续提升。
常见问题解答
Q1:精益车间现场管理的实施需要哪些前提条件?
A1:精益车间现场管理的实施需要建立良好的团队合作氛围,员工的积极参与和支持是关键。此外,需要有明确的改进目标和指标,以及有效的沟通和反馈机制。
Q2:精益车间现场管理是否适用于所有类型的生产环境?
A2:精益车间现场管理可以适用于不同类型的生产环境,包括制造业、服务业和办公环境等。然而,实施的具体方法和重点可能会有所不同,需要根据实际情况进行调整和定制。
Q3:如何评估精益车间现场管理的效果?
A3:评估精益车间现场管理的效果可以通过多种指标进行,如生产效率、质量指标、库存水平、员工参与度等。同时,可以进行周期性的评估和回顾,以持续改进和优化管理效果。