如何实施
精益生产更高效,实施精益生产更高效的关键在于全员参与、不断改进的文化以及适时采用精益工具。以下是一些建议:
1. 培训与意识普及:
-为员工提供精益培训,确保全员理解精益原理和工具。
-促使员工认识到精益对提高效率和质量的重要性。
2. 建立改进文化:
-建立鼓励改进的文化,鼓励员工提出改进建议,参与问题解决。
-创建一个安全、开放的环境,让员工愿意分享和尝试新的方法。
3. 价值流分析:
-进行价值流分析,识别和理解价值创造和非价值创造的活动。
-定位流程瓶颈和浪费,制定改进计划。
4.
5S管理:
-推行5S管理,即整理、整顿、清扫、清洁、素养。
-维护清洁有序的工作环境,提高生产效率。
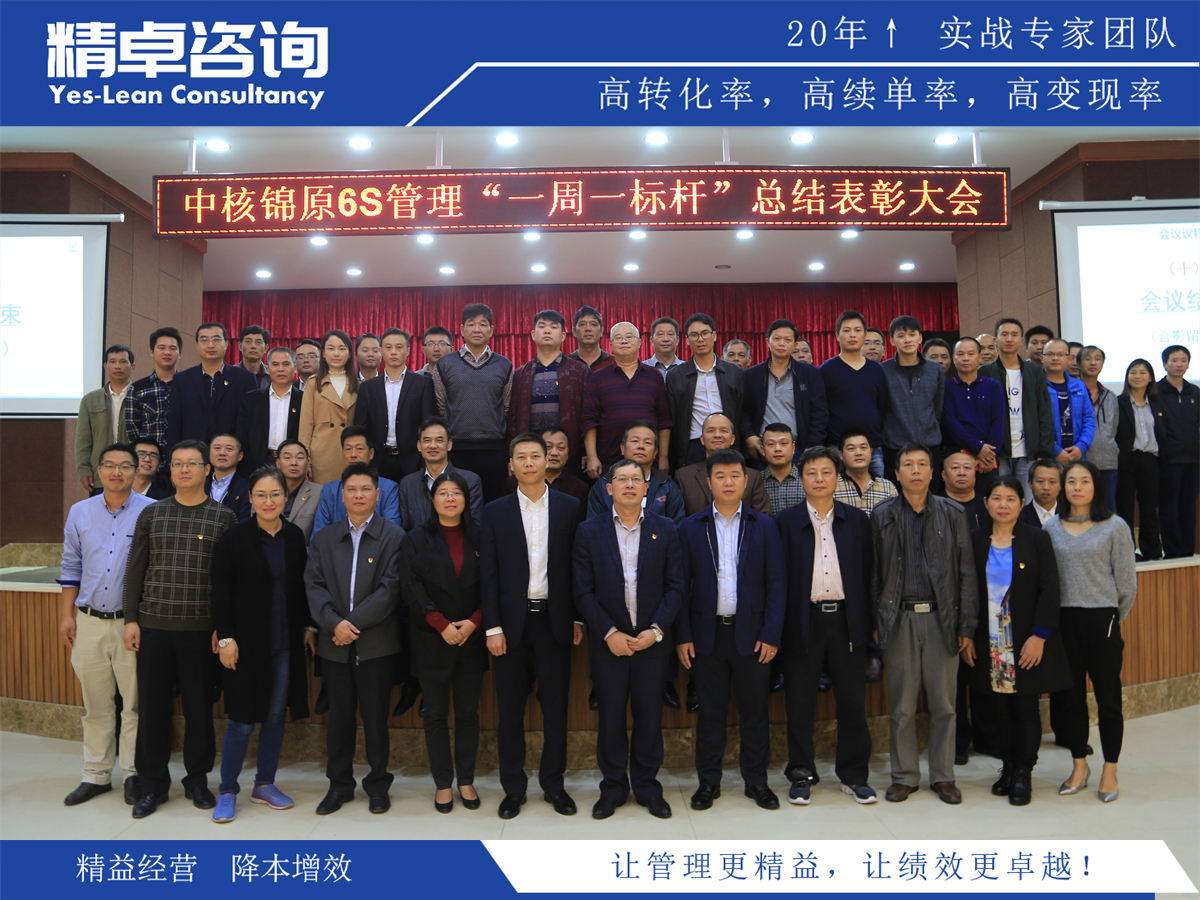
5. 流程改进:
-利用流程改进工具,如Kaizen(改善活动)、PDCA(Plan-Do-Check-Act)循环等。
-尝试小规模的改进,快速迭代,积累改进经验。
6. 单品流生产:
-实施单品流生产,减少库存和等待时间。
-提高生产线灵活性,按需生产,降低制造周期。
7. JIT生产:
-实施Just-In-Time(JIT)生产,按需生产,减少库存积压。
-与供应商建立紧密关系,确保及时供货。
8. 质量管理:
-强调零缺陷的生产理念,实施严格的质量控制。
-使用统计过程控制等方法,确保产品符合质量标准。
9. 度量和反馈:
-设定关键绩效指标(KPIs),定期评估生产绩效。
-提供实时的反馈,帮助团队识别问题并采取及时的改进措施。
10. 技术支持与数字化:
-利用信息技术和数字化手段,实现生产过程的监控和分析。
-使用先进技术提高工厂智能化水平。
11. 员工激励与奖励:
-设立奖励机制,鼓励员工提出创新性的改进建议。
-认可和奖励那些为提高效率和质量作出贡献的团队和个人。
12. 持续改进:
-建立持续改进的循环,将改进作为常态化的工作。
-定期进行改进会议,分享经验和学习。
通过以上措施,企业可以实现更高效的精益生产,不断提升效率、降低成本、提高质量,并更好地适应市场的变化。