精益生产管理体系旨在通过优化流程和减少浪费来提升生产效率和产品质量。其核心理念是最大化价值,最小化浪费,这不仅提高了生产效率,还降低了成本。本文将全面解析
精益生产管理体系的关键要素,包括价值流图的绘制、流程优化的实施、浪费识别与消除、持续改进的方法,以及如何通过精益文化的推广来实现全面的流程优化。通过这些方法,企业可以实现生产的精益化,获得竞争优势,并推动业务的可持续发展。
1. 精益生产概述
1. 精益生产定义
- 精益生产是一种管理理念,源于丰田生产系统,旨在通过精简流程、减少浪费和提升效率来优化生产过程。
2. 核心原则
- 价值定义:确定客户所重视的价值,以价值为中心进行改进。
- 价值流图:绘制和分析价值流图,以识别和消除浪费。
2. 价值流图的绘制与分析
1. 价值流图概述
- 图示内容:价值流图展示了从原材料到成品的整个生产过程,包括所有的步骤、信息流和物料流。
2. 绘制步骤
- 识别步骤:标识生产过程中的各个步骤,确定每一步的增值与非增值活动。
- 记录数据:收集各步骤的时间、成本和资源消耗数据。
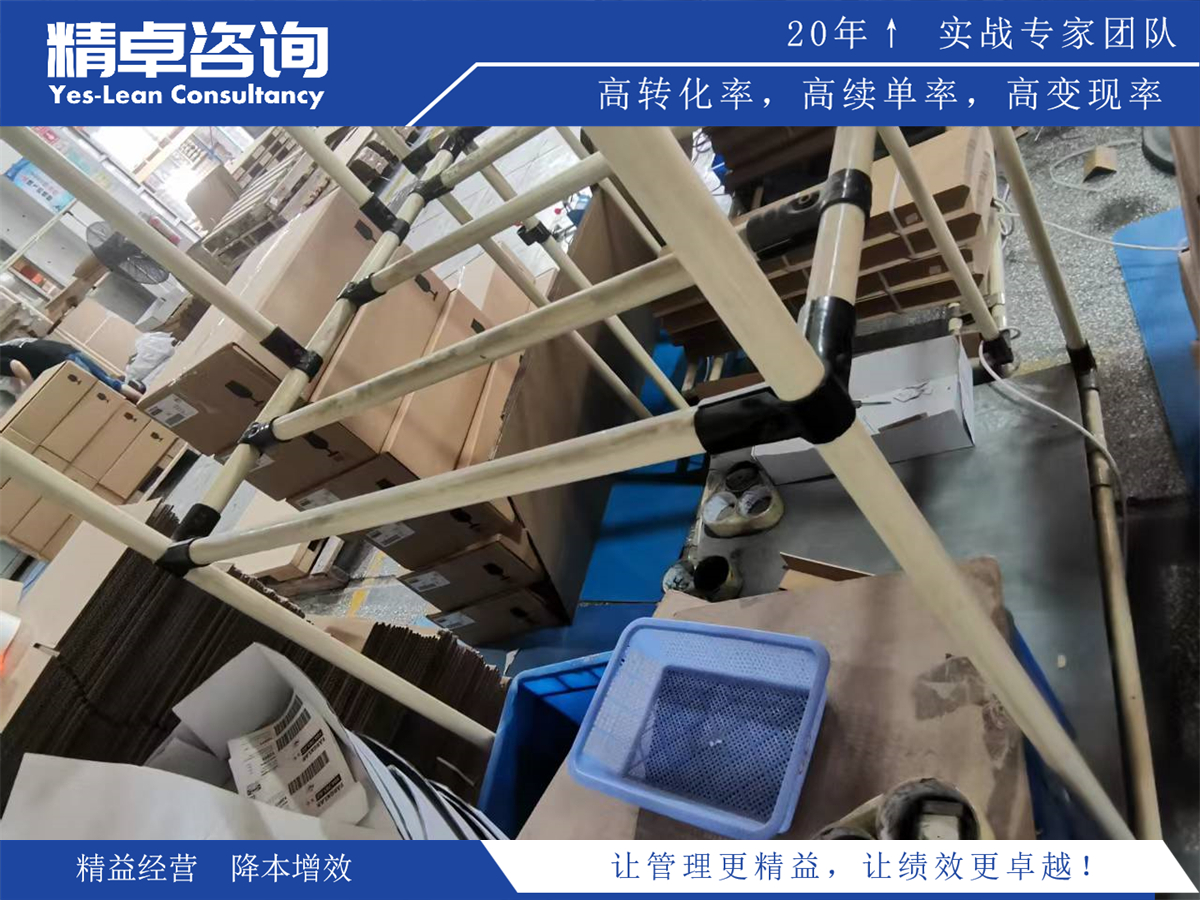
3. 分析与优化
- 识别浪费:找出价值流中存在的浪费,如等待时间、过度加工和库存积压。
- 优化方案:根据分析结果,提出改进建议,以提高流程效率和减少浪费。
3. 流程优化的实施
1. 流程设计
- 标准化作业:制定标准化作业流程,以确保一致性和高效性。
- 拉动系统:采用拉动生产系统(如看板系统),以减少库存和生产过剩。
2. 精益工具
- 5S:整理、整顿、清扫、清洁和素养,通过规范化操作环境提高效率。
- 价值 Stream Mapping (VSM):用于绘制和分析价值流图,帮助识别和改进生产过程中的瓶颈和浪费。
3. 瓶颈管理
- 瓶颈识别:确定生产过程中的瓶颈环节,通过提升瓶颈环节的效率来提高整体生产能力。
- 改进措施:应用改进措施,如增加设备、优化操作方法或调整工作负荷。
4. 浪费识别与消除
1. 浪费类型
- 七大浪费:生产过剩、等待时间、运输、过度加工、库存、动作和缺陷。
2. 消除浪费
- 根本原因分析:通过分析浪费产生的根本原因,采取措施进行改进。
- 持续改进:实施持续改进策略,如PDCA循环(计划-执行-检查-行动),以不断优化生产流程。
5. 持续改进的方法
1. Kaizen(改善)
- 小步改进:鼓励员工提出改进建议,进行小规模的逐步改进,推动持续进步。
- 团队参与:组建改进团队,开展改进活动,推动全员参与的精益文化。
2. 绩效评估
- 指标监控:设定和监控关键绩效指标(KPI),评估精益措施的效果。
- 反馈机制:建立反馈机制,及时调整改进策略和方法,确保持续改进。
6. 推广精益文化
1. 文化建设
- 领导支持:确保高层管理者支持精益文化,推动组织变革和改进。
- 员工培训:开展精益培训,提升员工对精益理念和工具的理解和应用能力。
2. 成功案例分享
- 案例学习:分享成功的精益生产案例,激励员工参与和实践精益理念。
- 经验交流:定期组织经验交流活动,促进最佳实践的传播和学习。
结论
精益生产管理体系通过优化流程和减少浪费,提高了生产效率和产品质量。通过价值流图的绘制、流程优化、浪费消除、持续改进和精益文化的推广,企业能够实现生产的精益化,提升竞争力,并实现业务的可持续发展。这一体系不仅关注生产效率的提升,还注重员工的参与和企业文化的建设,是推动企业全面提升的重要工具。